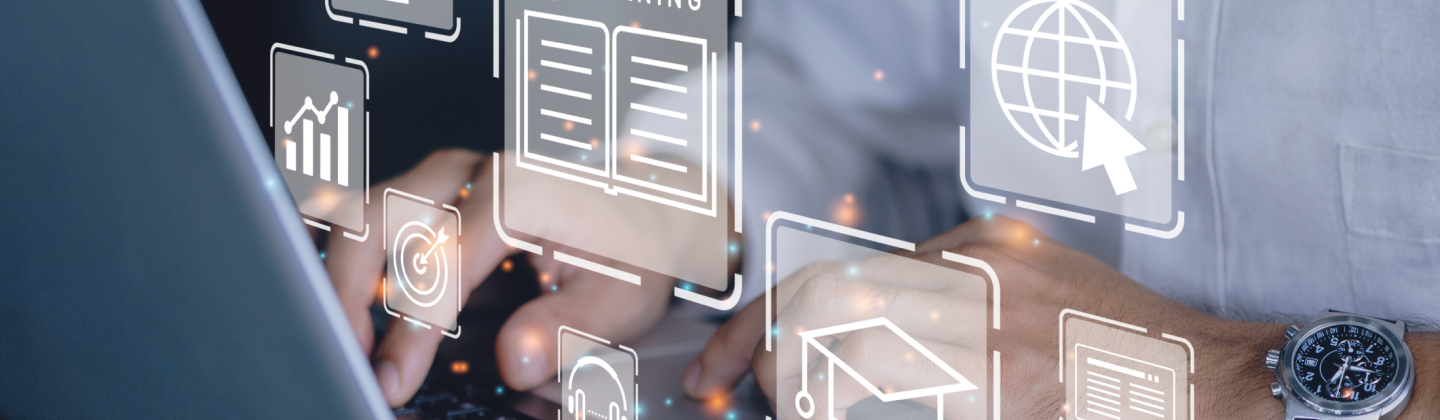
Success Stories
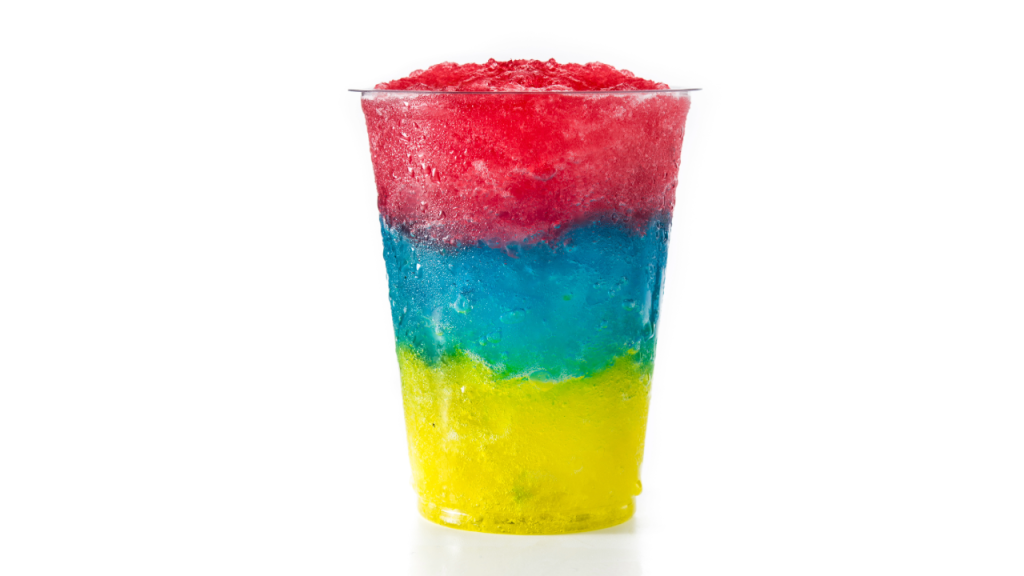
Mary Mack’s Facility is SQF Certified for Floss Sugar, Frozen Lemonade, and Syrups Manufacturing
View Success story

FDA and USDA-Inspected Food Manufacturer and Distributor RC Fine Foods Gains SQF Certification
View Success story
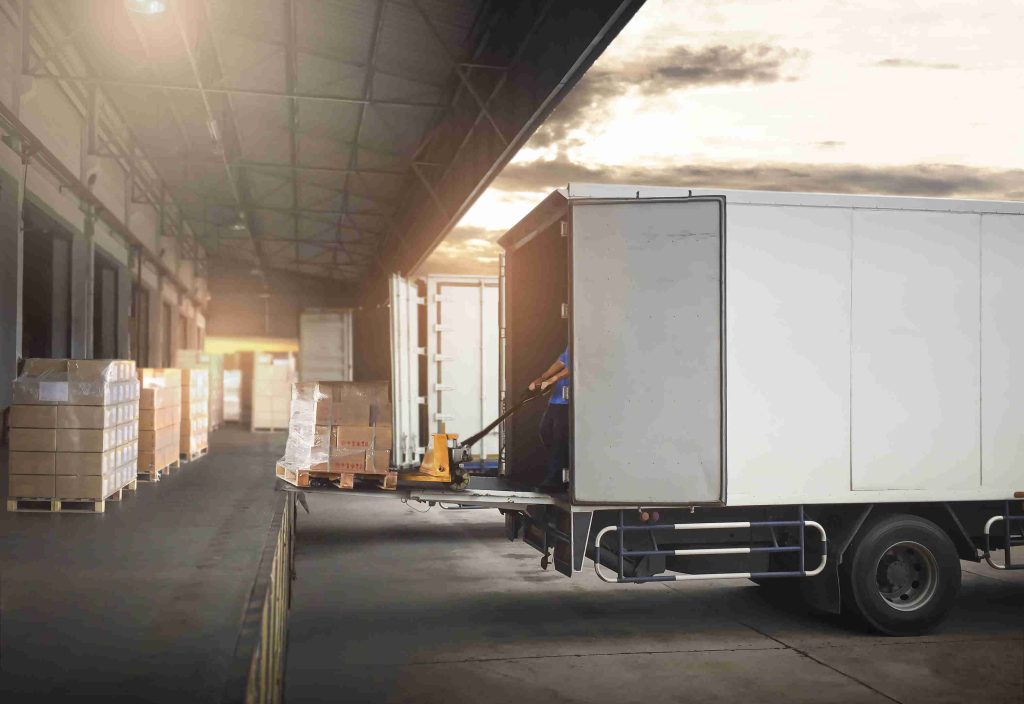
Three Storage & Distribution Facilities in Three States Achieve SQF Certification on the First Try
View Success story
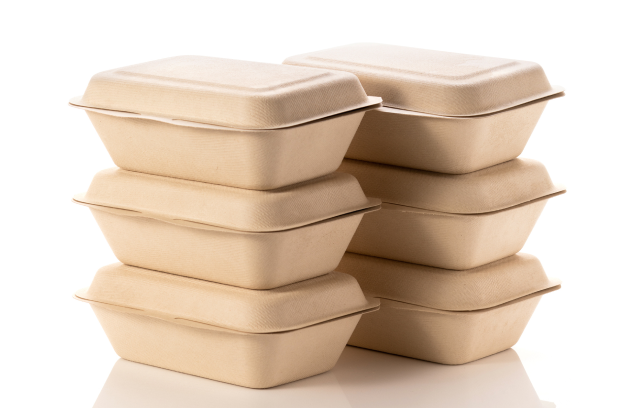
Packaging and Printing Company Passes ISO 9001: 2015, SQF, and FSC Certification Audits
View Success story
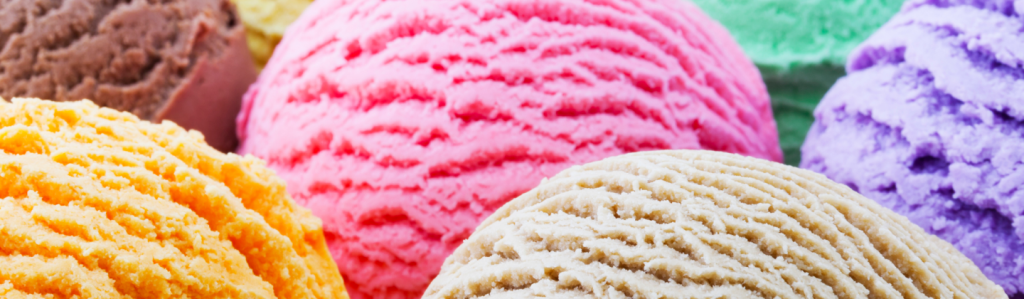
Hershey Creamery Company Achieves SQF Certification to Support Their Continued Growth
View Success story
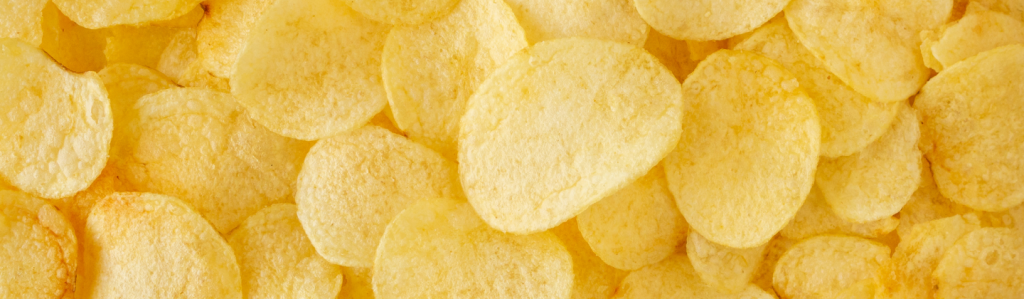
Conn’s Chips Receives SQF Certification & Gets on the Shelves of Big Box Retailers
View Success story
Learn From Our Clients’ Experiences
Three Facilities SQF Certified in Three States on the First Try
We used Kellerman Consulting to assist with the creation, documentation and implementation of our food safety plan on the path to SQF certification in three busy warehouses simultaneously in three different states. Because of the incredible level of detail and individualized support provided by the Kellerman Consulting team, we were able to achieve certification in all three on the first audit with only a handful of minor non-conformances noted. The team also provides excellent guidance and advice on all follow-up actions needed. I highly recommend this team to anyone that is looking for help navigating all the complexities around SQF certification, they played a substantial role in our success in this process.
Jake Jackson, Director of Supply Chain, Rainforest Distribution
SenSource Global Sourcing Gains ISO 9001:2015 Certification
"The entire process has been smooth for us. From inquiring about the consulting service to getting assigned a consultant to actually working with the consultant before, during, and after the audit, everything has exceeded our expectations. Kellerman Consulting staff are personable and professional, very knowledgeable about ISO, and were willing to work around some tight scheduling requirements on our end. Tim, specifically, was a rock star for us. We appreciated his understanding of the ISO regulations, his experience in the world of auditing, and his flexibility in meeting our varying scheduling needs".
DeAnna Highfield, Project Assistant & Compliance Analyst
AOA Products has SQF and ANSI Dietary Supplement Audit Success
Kellerman Consulting has assisted AOA with our SQF program and most recently with our ANSI dietary supplement program. The contract packaging in the supplement market is new to AOA, and without Kellerman Consulting's professionalism, kindness & dedication we would not have been able to achieve the near perfect score on our audits . Kellerman Consulting was with us during every step of the process including assisting us in the simplification of our binders to include our programs all in one. Lastly, helping us through any auditor's non-conformance obstacles. Kellerman Consulting were there to help guide us to not only passing but passing with high scores and minimal non conformances.
AOA Products, LLC highly recommends Kellerman Consulting to anyone in need of consulting services.
Joshua Albright, AOA Products, LLC
FSQA Manager is Trained in Four Months to Pass Their First BRCGS Audit
Kellerman Consulting does an amazing job of consistently meeting customers’ expectations and taking time to understand the needs of their unique customer. Their service goes above and beyond expectations. I had come to Shelby Foods just 4 months before the initial BRCGS audit and had very little idea what was required for BRCGS. Brian worked with me and patiently answered all my questions until I understood everything.
We have an A rating with BRCGS and I attribute that to Brian Kellerman and Kellerman Consulting for everything they have done to help our business to get the certification. Their initial assessment of our company, the documents, and information provided to make our
plan were great. During the audit it gave me confidence knowing we had everything in line with BRCGS requirements.
Tammy Neyer, FSQM Shelby Cold Storage /Shelby Foods LLC.
Clarendon Flavors’ New SQF Practitioner is Trained in Three Months for SQF Success
“Kellerman Consulting made a world of difference in both the time and quality of implementation of our SQF program at Clarendon Flavors. Honestly, we would have had a very tough time doing it without their expertise. When I took over the position of SQF Practitioner at our company with no prior experience, I had only 3 months to prepare for our first SQF Audit. Tim and Brian rallied around me and made sure I was ready to meet the challenge head on. From writing and reviewing documents, to educating a complete novice, to performing a mock audit in advance, the Kellerman team made sure we were ready not only to pass, but to score a 91 on our first audit. I could not recommend them more highly”!
Benjamin A. Jones, Manager, QA and Regulatory Affairs
Lomo Cold Storage Receives 99.37% on Their GDP Audit
Our Kellerman Consulting Food Safety Consultant, Tim Grady, was incredibly patient and supportive throughout the entire process of helping Lomo Cold Storage, LLC prepare for our GDP 3rd party audit. We got through our audit and we are very proud to have received a 99.37% score. I have been working for many, many years and it is very refreshing to work with someone that can be so professional and do what they say they will do and still treat people with kindness.
Edie Hensen, Lomo Cold Storage, LLC.
Omakase Restaurant Group Receives Support for HACCP Plans & FSMA Program
Kellerman Consulting went above and beyond to make sure we had everything we needed for our ROP, Sous Vide, Cook Chill, & FSMA Program! They're very detail oriented and covered more ground than I even anticipated.
Charlie Weintraub, Director of Operations BOH | Dumpling Time Brand
Caprock Pecans Obtains 99% on their PrimusGFS Audit After Working with Kellerman Consulting
"Jaime with Kellerman Consulting wrote a great PrimusGFS program, and I continue to profit from it. We got a 94% before corrective action and a 99% final score".
Kirk Layton, Owner of Caprock Pecans
Patty Wagon Express Complies with FSMA to Grow Their Wholesale Business
I highly recommend working with Kellerman Consulting. Working with Brian Kellerman put me at ease. He’s very informative, patient, and took the time to walk me through the process. An all around good guy! If ever I need the services this company provides I’ll look no further.
Andre Yorke, Owner of Patty Wagon Express Inc.
Strong Spas Passes Their Costco Non-Foods GMP Certification Audit
“Kellerman Consulting was professional, efficient, and continues to show their support and guidance even after the GMP audit”.
Malisa Reynolds, Quality & Compliance Manager Strong Spas.
Beach Cooperative Grain Achieves Excellence on Their SQF Audit
“Working with Kellerman Consulting was the best decision my company’s SQF Team could have made. The professionalism, passion, and knowledge their consultants have, made the experience a 20/10! Not only did our audit score reflect how great their system works, but I also gained so much more understanding of SQF and confidence as a Quality Manager!”
Ashley Tescher, Beach Cooperative Grain | QA & Compliance
Folding-Carton Company, Everett Graphics, Obtains a Nearly Perfect Score on Their SQF Audit
“Kellerman Consulting acted as a trainer for our new QC hire, so we benefited from that as well as the successful preparation for the SQF audit. We got a 98% on the audit. That should speak for itself. You need to use these people. We looked at a number of consulting organizations and I’d go out of my way to recommend Kellerman Consulting”.
Mark Carlson, VP Business Operations | Everett Graphics
Apex Outdoor LLC Receives Approvals From USDA Regional Manager for Their HACCP Plans
Kellerman Consulting came to the rescue for me after working with another competitor who left me in the dark. I was so relieved to find a responsible, knowledgeable consulting firm who could help a new operator out in developing a full blown HACCP plan - and teach me along the way! Kellerman Consulting held my hand every step of the way (and trust me I needed it)! Kellerman Consulting got me through all of my approvals with an easy to follow HACCP plan that appeased a USDA regional manager.
Steven McBee, CEO/Co-Owner - McBee Farm & Cattle Co & Apex Outdoor LLC
Roka Akor gets ROP HACCP Plan Approved
They are a pleasure to work with. I have a lot to do and am very busy – they outlined everything out in a very reasonable fashion and got the job done in the precision and detail we needed it to be. I would work with them again!
Ben Uvodich, Regional Manager, Roka Akor
Outer Aisle Gourmet Achieves SQF Certification for Three Sites
“We partnered with Kellerman Consulting very early on in the SQF certification process, and by relying on their expertise and methodical approach to collecting, compiling, and organizing the required documentation, we were successful in gaining our certification. I would highly recommend Kellerman Consulting to anyone considering this type of certification for their organization”.
Jennifer Lawrence, Director Of Operations | Outer Aisle Gourmet
Premier Printing Corp Receives an Excellent SQF Audit Score on Their First Try
“They are just down-to-earth real-world guys that happen to be experts. We came out with a great score to keep a major client and our competitive edge with their guidance and expertise”.
Jeff Trombo, VP of Premier Printing Corporation
Joe Granato Produce has Their BRCGS Program Converted to an SQF Program to Keep Key Business
I couldn’t have asked for a better company to help us work on our certification. They were helpful, educational, and got our program successfully converted with clear professionalism.
Matt Granato, VP of Joe Granato Produce
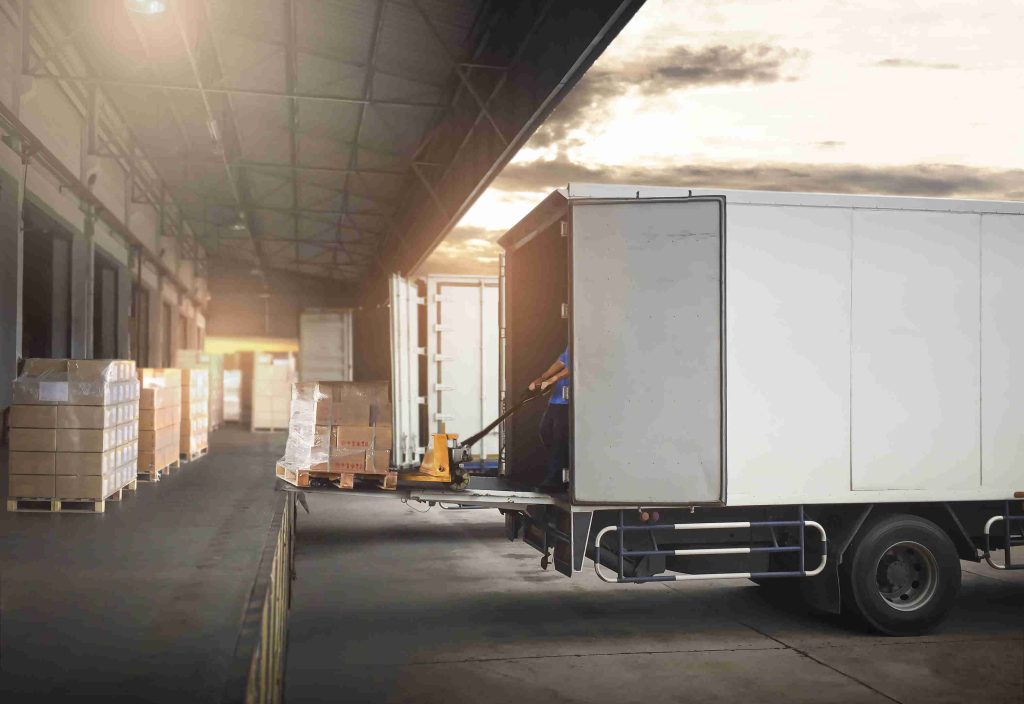
Three Facilities SQF Certified in Three States on the First Try
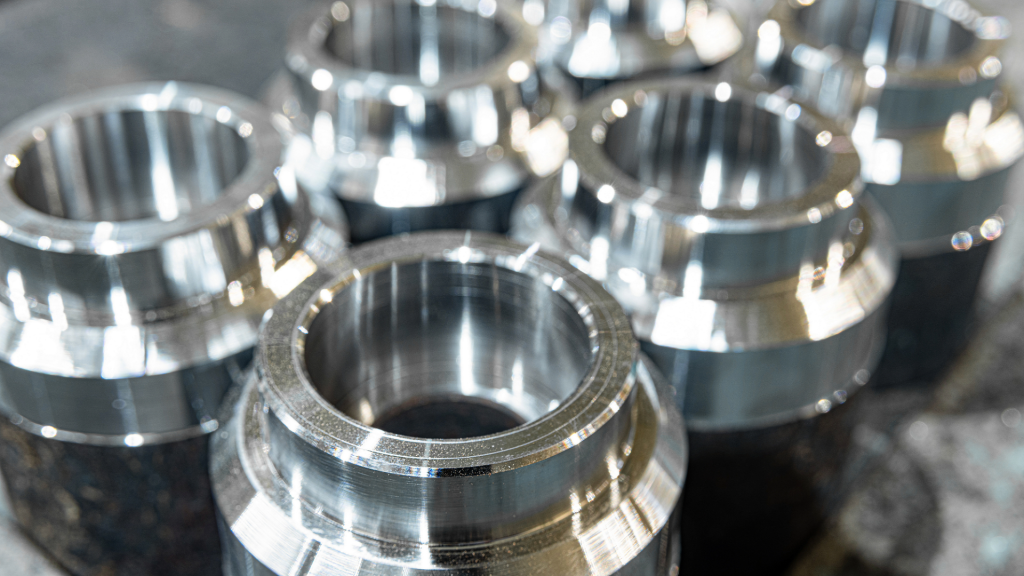
SenSource Global Sourcing Gains ISO 9001:2015 Certification
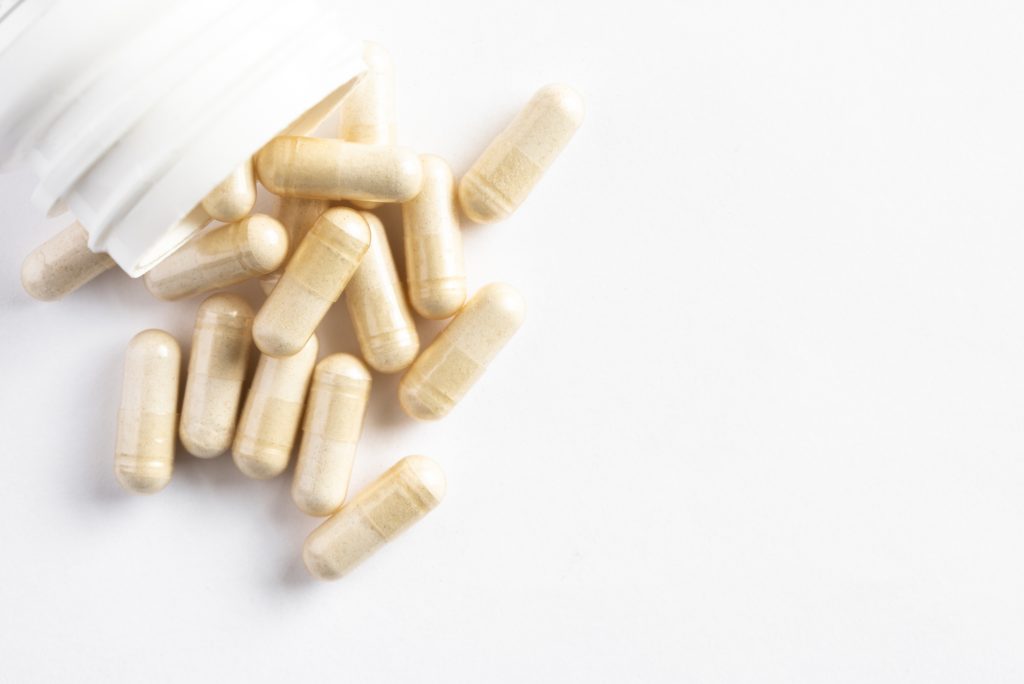
AOA Products has SQF and ANSI Dietary Supplement Audit Success
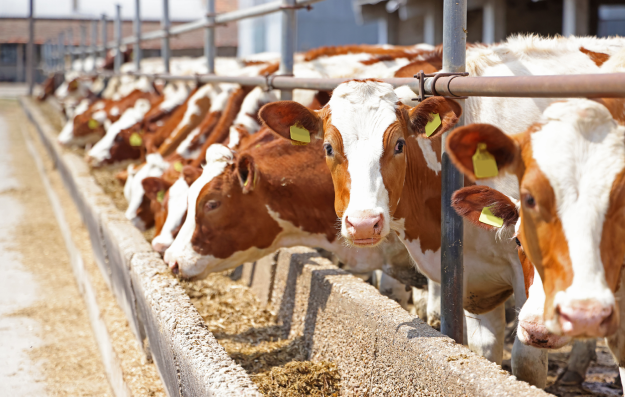
FSQA Manager is Trained in Four Months to Pass Their First BRCGS Audit
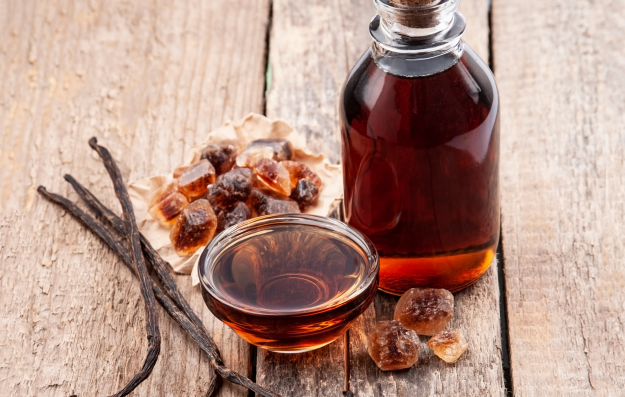
Clarendon Flavors’ New SQF Practitioner is Trained in Three Months for SQF Success
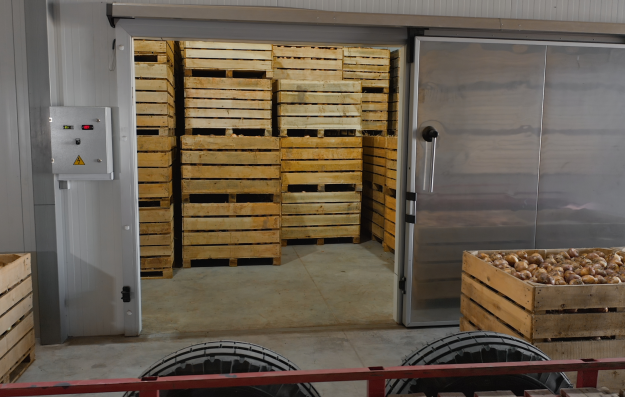
Lomo Cold Storage Receives 99.37% on Their GDP Audit
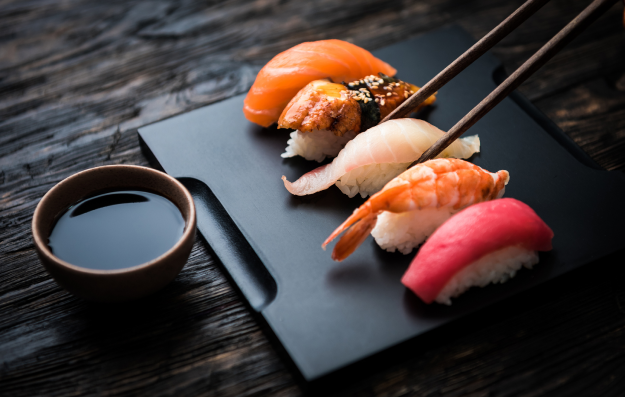
Omakase Restaurant Group Receives Support for HACCP Plans & FSMA Program

Caprock Pecans Obtains 99% on their PrimusGFS Audit After Working with Kellerman Consulting
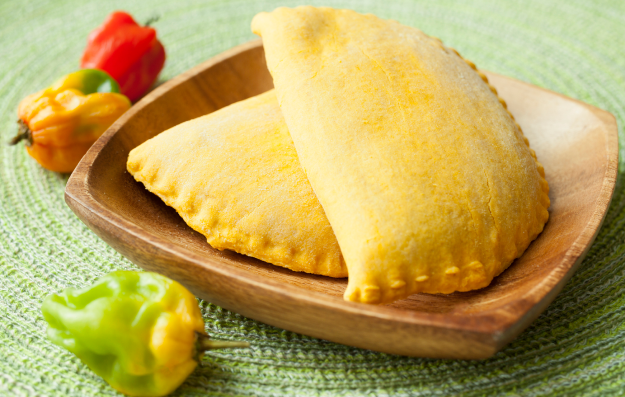
Patty Wagon Express Complies with FSMA to Grow Their Wholesale Business
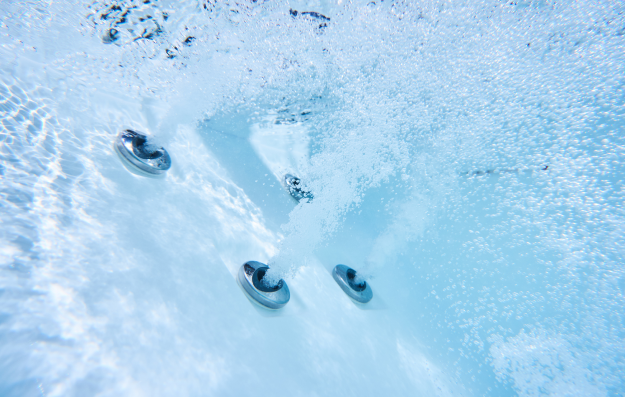
Strong Spas Passes Their Costco Non-Foods GMP Certification Audit
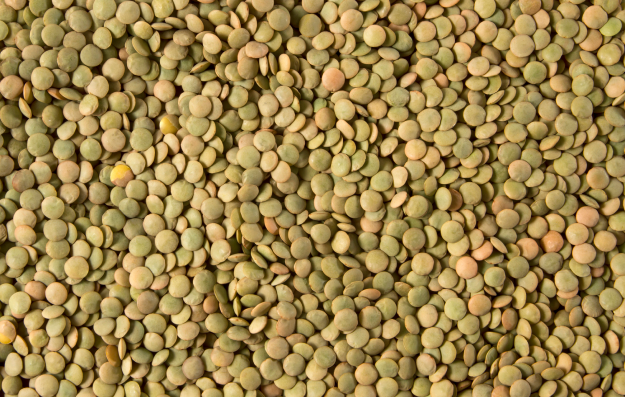
Beach Cooperative Grain Achieves Excellence on Their SQF Audit
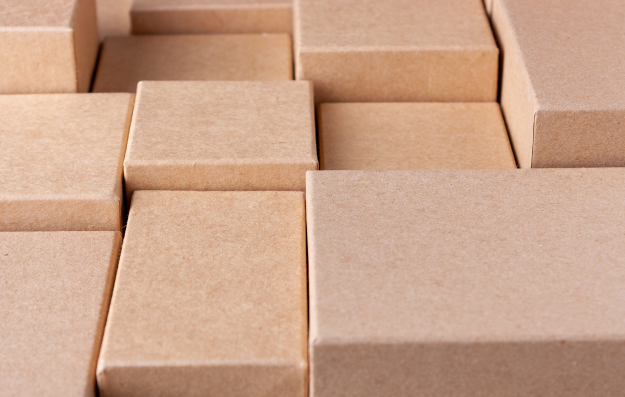
Folding-Carton Company, Everett Graphics, Obtains a Nearly Perfect Score on Their SQF Audit
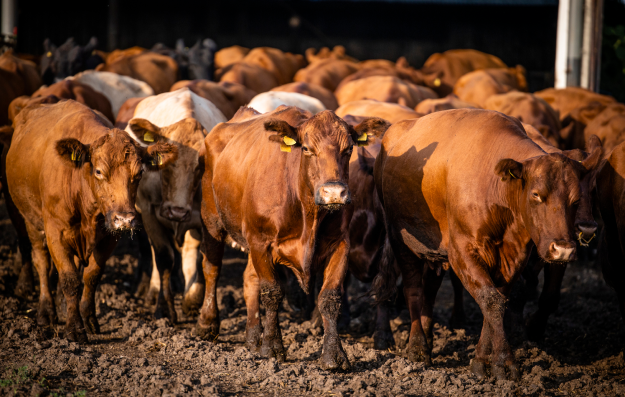
Apex Outdoor LLC Receives Approvals From USDA Regional Manager for Their HACCP Plans
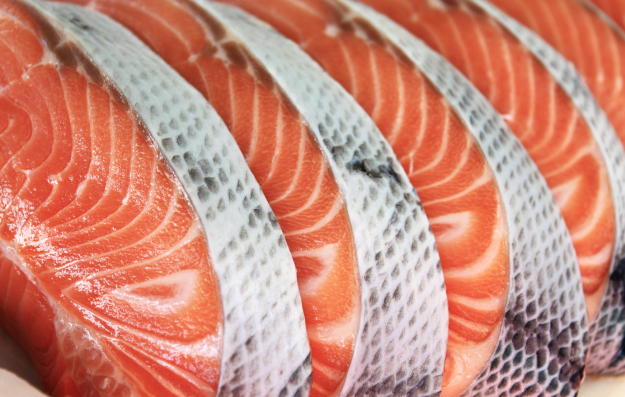
Roka Akor gets ROP HACCP Plan Approved
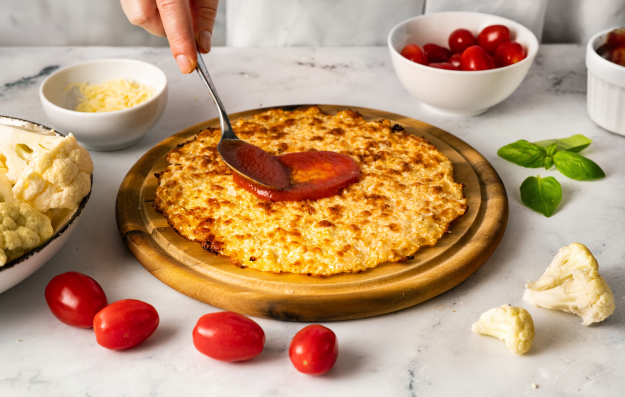
Outer Aisle Gourmet Achieves SQF Certification for Three Sites
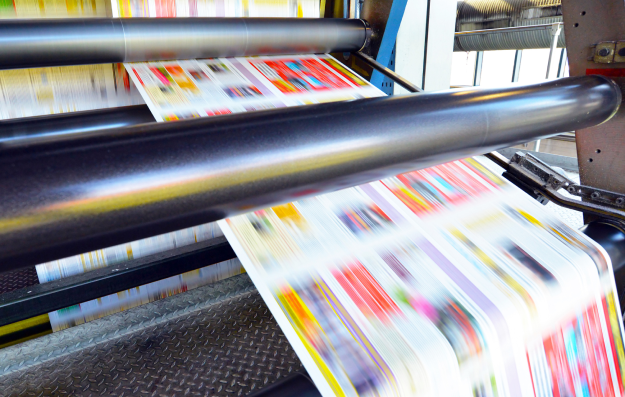
Premier Printing Corp Receives an Excellent SQF Audit Score on Their First Try
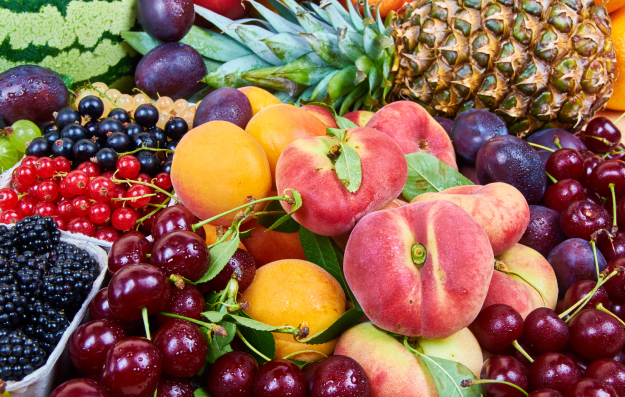
Joe Granato Produce has Their BRCGS Program Converted to an SQF Program to Keep Key Business
Questions about costs, timelines and requirements?
Contact Us Today for a Free Consultation
Available to travel for your project
-
Headquarters
-
Offices