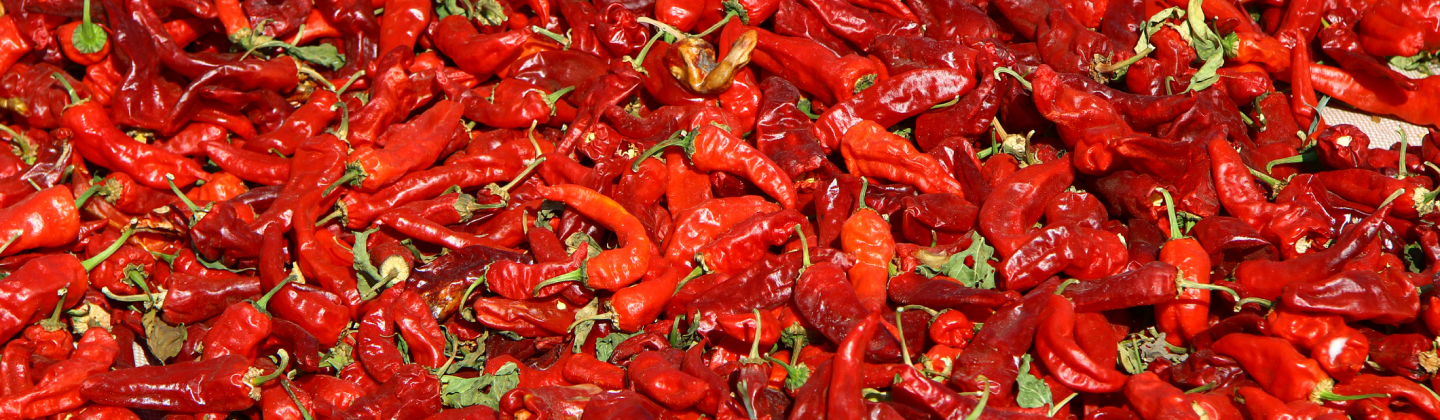
Creating New Business Opportunities by Achieving an SQF Certification
A dried spice manufacturer in the western U.S. needed to achieve an SQF certification within an aggressive timeline in order to attain a new customer and increase market presence.
The Overview:
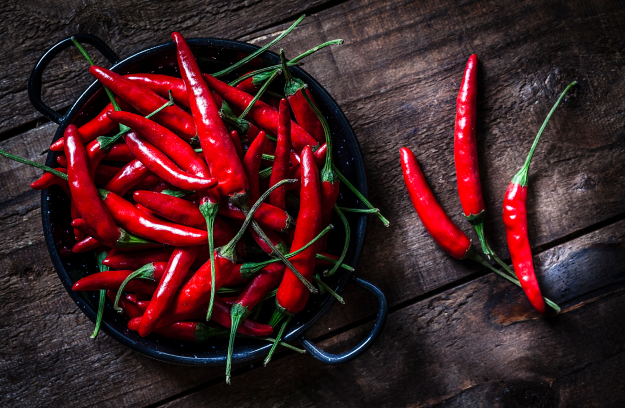
The Result:
Successful implementation of the SQF Program and passing of the audit on the first try to achieve the certification required by the new customer.
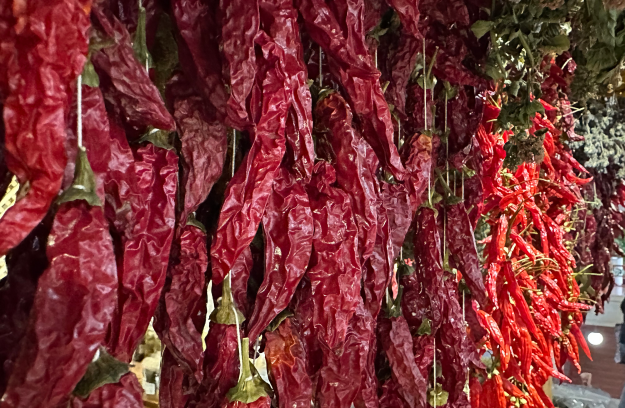
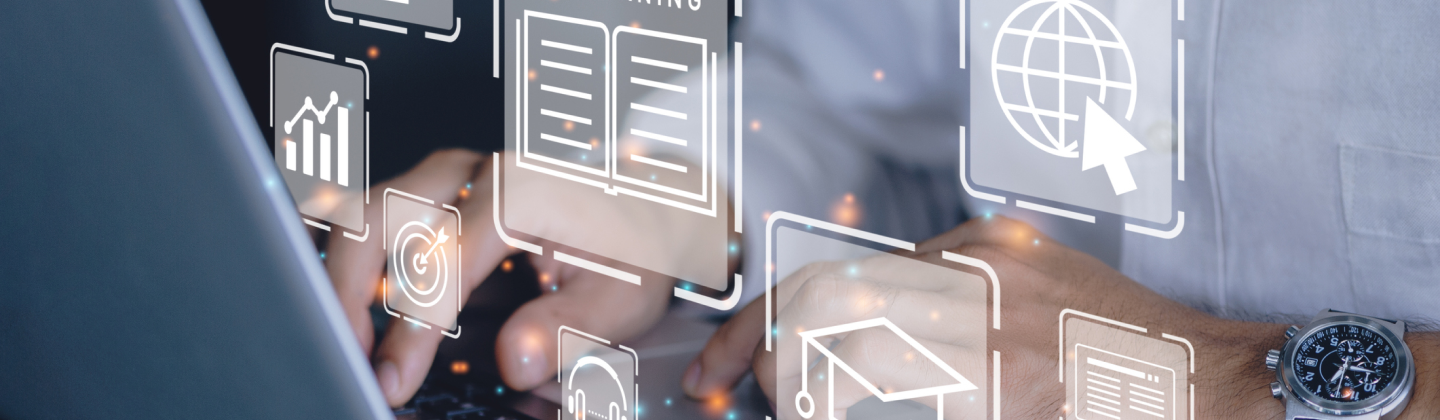
The client successfully completed their SQF certification audit within their target timeframe and achieved a very high score under the SQF Edition 9 standard.
Facing a similar challenge? Click the button below to get in touch.
Questions about costs, timelines and requirements?
Contact Us Today for a Free Consultation
Available to travel for your project
-
Headquarters
-
Offices