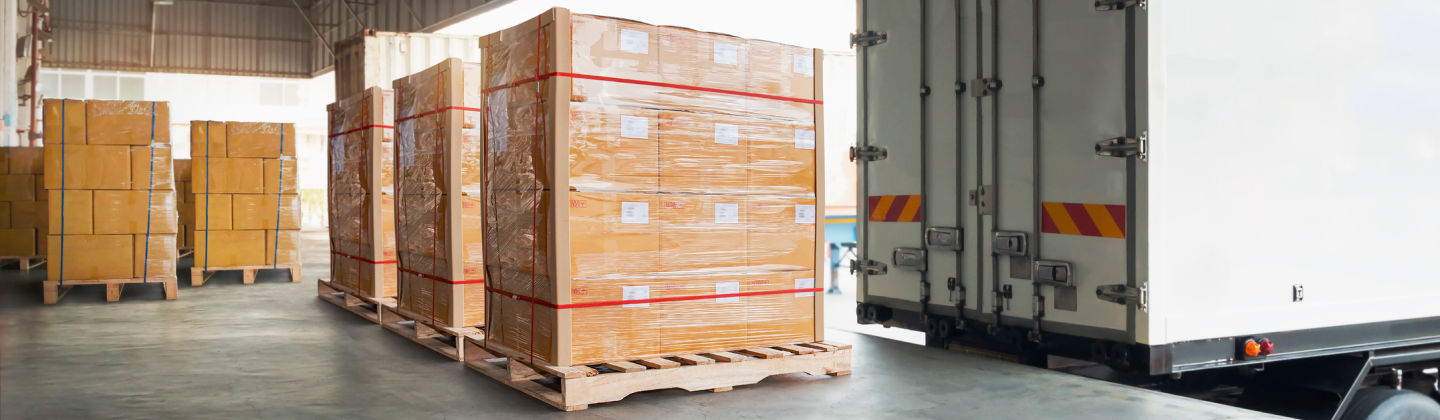
Converting From a BRCGS Program to an SQF Program Kept Key Business
The Overview:
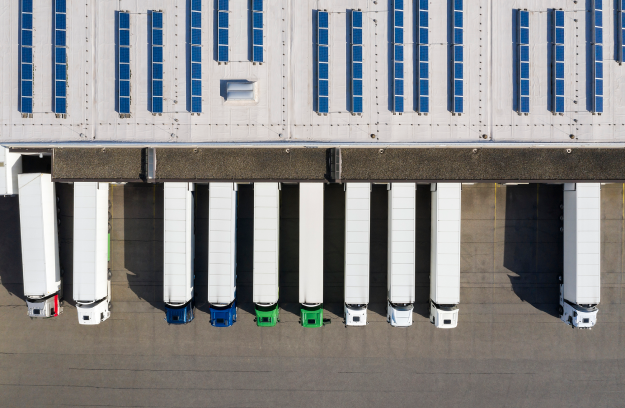
The Result:
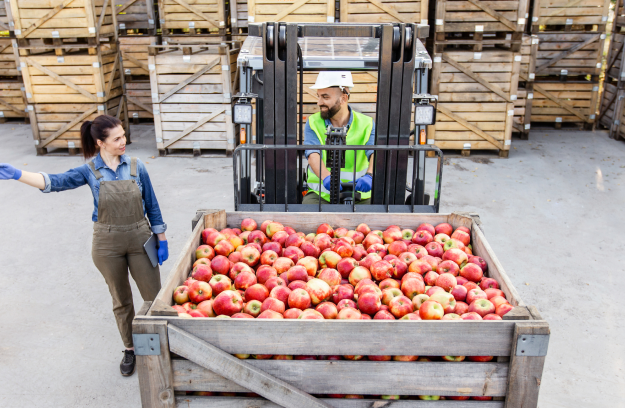
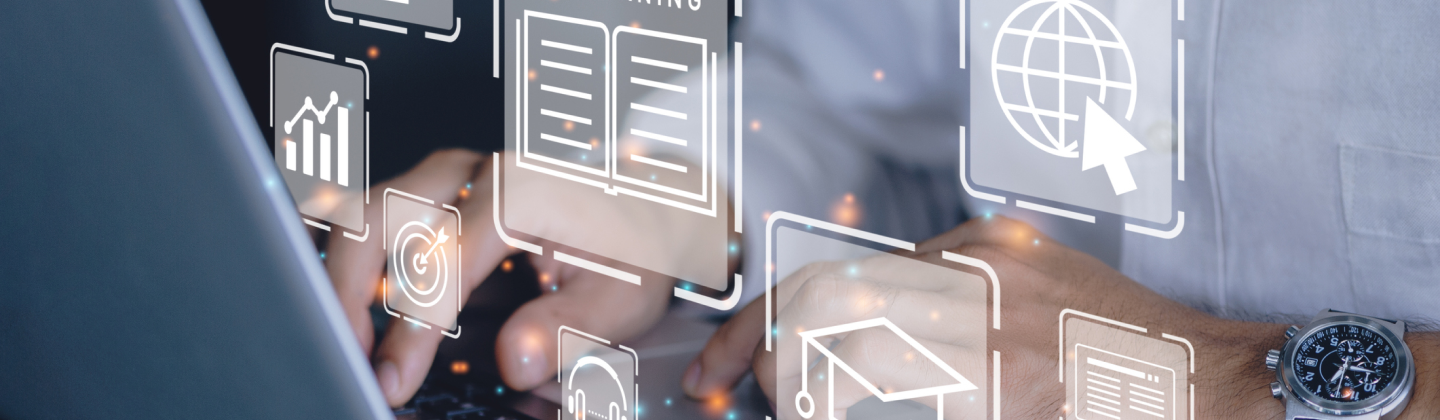
The facility got a passing grade on the SQF audit allowing for a 12-month recertification.
Facing a similar challenge? Click the button below to get in touch.
Questions about costs, timelines and requirements?
Contact Us Today for a Free Consultation
Available to travel for your project
-
Headquarters
-
Offices