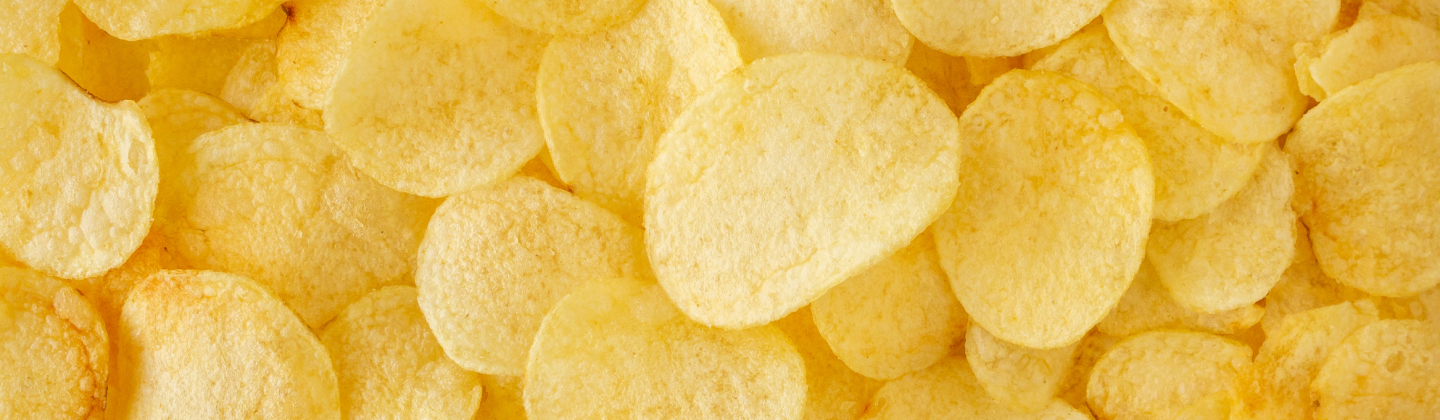
Conn’s Chips Receives SQF Certification & Gets on the Shelves of Big Box Retailers
The Overview:
- Conn’s was operating out of an older facility and had initial concerns about the ability of the facility itself to become compliant with SQF expectations.
- Third-party food safety expectations were relatively new to the operation as they had only previously been held to FDA standards
- The business co-manufactures a variety of products for multiple different entities alongside the production of their own labeled products, therefore this also required consideration with their SQF program.
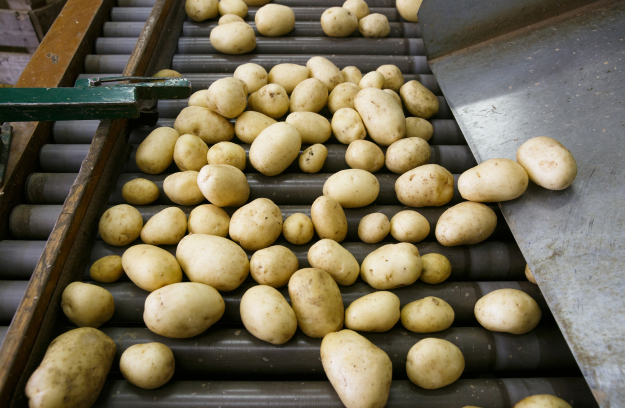
The Result:
Conn’s passed their first ever third-party food safety audit on the first attempt.
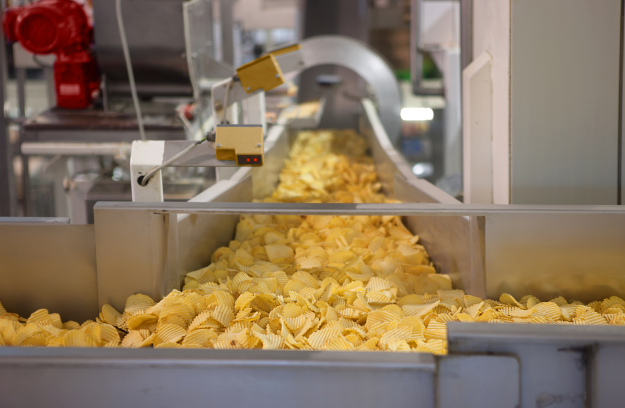
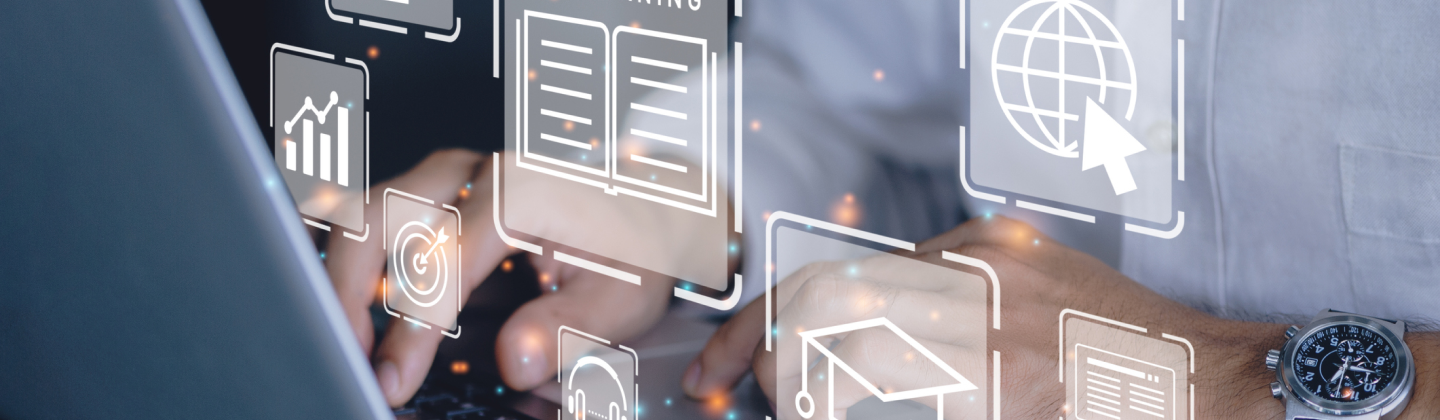