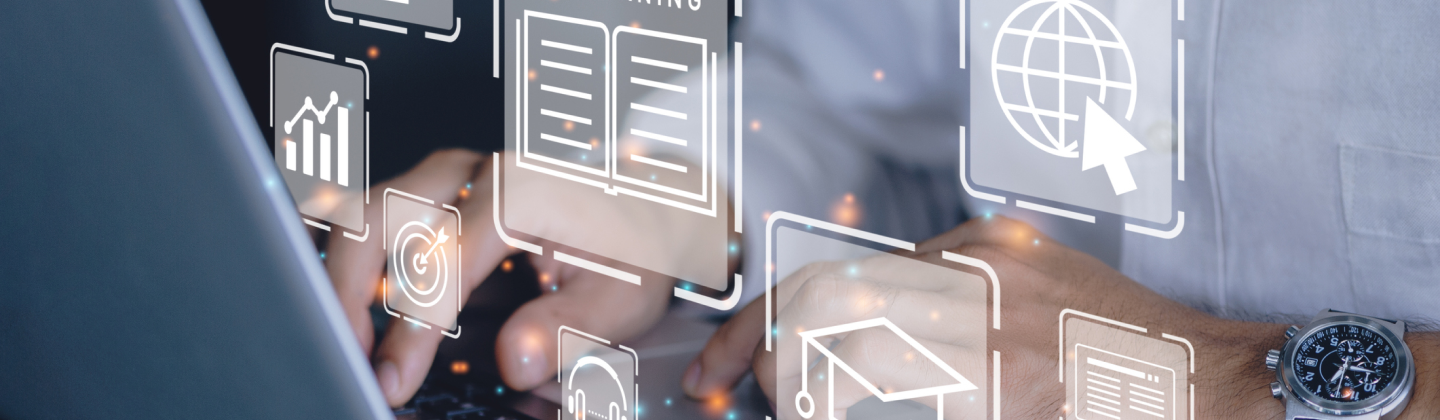
Episode 2: Invalid Processes and Signs of Invalidation
Episode 2: Invalid Processes and Signs of Invalidation
Welcome to the second video in Kellerman Consulting’s series on validation and verification in manufacturing operations. In our previous episode we introduced what validation and verification are and who should expect to perform these functions.
Validation is a complex concept, and it is not an easily defined or understood idea, and in this video we are going to further define what validation is by looking at what it is not. What I mean here is that we are going to talk about broken or damaged processes.
Invalid Processes
Invalid processes fail to work because they were either not planned correctly or conditions changed at some point so that the actions which previously worked correctly no longer work as intended. Because invalid systems are often the source of frustration, stress and even panic, we don’t often like to think or talk about these experiences for a business, and we’d prefer to just forget they ever happened. Let’s look at things that don’t work, and from there get a better understanding of what it means for things to work correctly.
Signs of Invalidation
When a consultant at Kellerman Consulting walks through a client’s warehouse and finds pallets being stored in aisles between rows of racking, our immediate assessment is that the space in the warehouse is invalid, otherwise, there would be space available on racking and off of the floor. That doesn’t mean that the facility is in trouble, or there’s something wrong with the facility, but we do expect there to be damage to racks, incorrect pulling of ingredients, damaged ingredients and injuries in the facility as a result of having to store materials this way. It’s an invalid condition. Every dent in the walls and all of the damage to equipment can be traced back to the fact that there is either not enough space, the wrong people, the wrong equipment or incorrect organization in the facility. That is invalidation. When you don’t see invalidation, then you probably have a valid system.
Choice of Equipment Causing Invalidation
For manufacturing operations this can also be seen in having the wrong production equipment. If I need to process 5000 lbs of ingredients for bread, and all I have is a small stand Hobart mixer, it will take around 50 batches to mix it all up. Over the course of those hours, and all of that loading and unloading of the stand mixer to work through it, it will not only cause the mixer to break down faster, but staging dozens of batches almost always leads to human error, and seemingly random problems, like spills or mislabeling that are not really random at all, and can be expected over a long range of runs.
A facility that has a form, fill and seal machine ready for use, only to discover that a new product does not work in the machine, resulting in hand packaging set ups, has been through an invalidation event. The machine was not correct for the project, but the sales people, operations people or management did not fully understand what they were committing to at the time of saying yes to the pack out. Having workers perform a hand pack while fancy equipment sits idle next to the line is not wrong, and ownership and management can agree to take on appropriate projects to keep workers busy with work, but the consequences of this invalidation are greater than are often realized while the team is just trying to get through the hand pack shift.
The biggest problem in a situation like the too small hand mixer, or the hand pack line is that the actions have not been forecasted correctly for time, or for manpower. Invalidation in one part of the facility, like a pack line, often requires pulling employees from other parts of the facility, like storage and distribution employees, or requires temporary employees and puts strain pressure on other parts of the facility that may not be directly connected to the invalidation event.
Verification of Invalidation
Once we start looking for these invalid events, we can start to find them all over a facility. Signs of invalidation, which we could also call verification of invalidation, would include events such as confusion in GMP areas where there are unlabeled containers or excess materials lying around, disorganized tools, or running out of key materials like hairnets, gloves, smocks or aprons.
Other verification may include frequently malfunctioning or broken equipment, water buildup, electrical outages, broken handles on containers, bent utensils, foundation cracks, excessive rusting of metal. Lastly, invalidation is verified through high staff turnover, frequent customer complaints, regulatory violations and regular unexpected capital shortages. Businesses use workarounds to deal with these circumstances, and those workarounds are functional for a time, but inevitably get damaged and breakdown, resulting from the underlying invalidation.
Once the negative results of invalid processes are observable, employees are left to attempt to address the symptoms of the invalidation, long after it is too late to prevent it from occurring in the first place.
Resources to Assist with Validation & Verification
Kellerman Consulting offers free food safety & quality training videos that cover environmental monitoring, controlling allergens, how to properly identify and document corrective and preventive actions, and also how to perform internal audits. I recommend reviewing those as part of thinking through validation in your program.
We also recommend taking some time and walking through your facility to look for signs of invalidation we have talked about. You may also consider doing some paperwork reviews for customer complaints, operational errors or Human Resource reviews to look for signs that you have an invalid program. Where you find evidence of this being the case, take some time to think through what part of that system or area is incorrect, and why it might be incorrect.
Free Validation & Verification Assessment Log Download
In our next video, we’re going to get back to looking at validation and verification, and we’re going to focus on long term sources of validation including the facility itself, the layout of infrastructure and major equipment.
If you would like to discuss having Kellerman Consulting write and implement your food safety and quality management system program, contact us for a free consultation.
Validation & Verification Resources
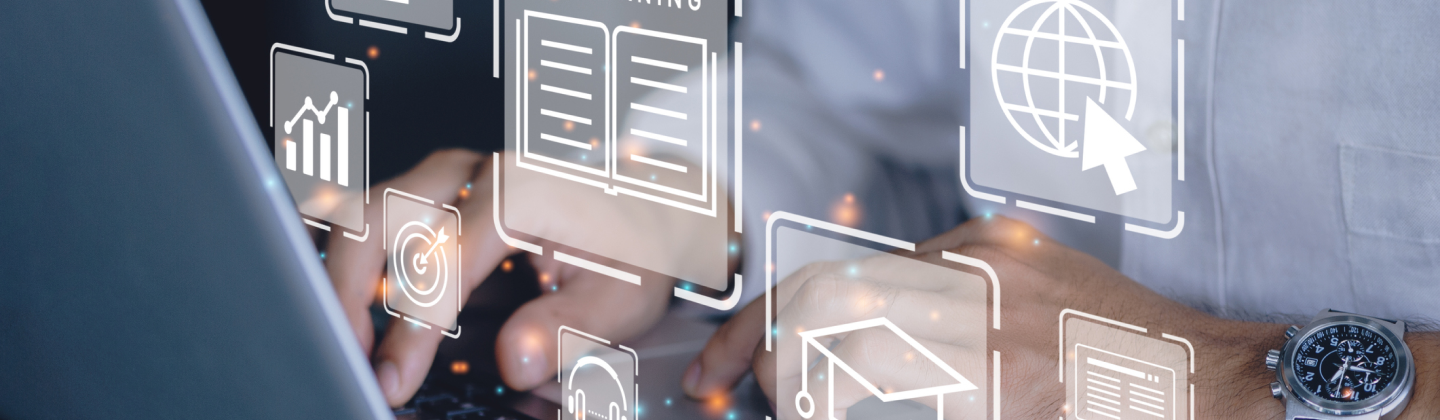