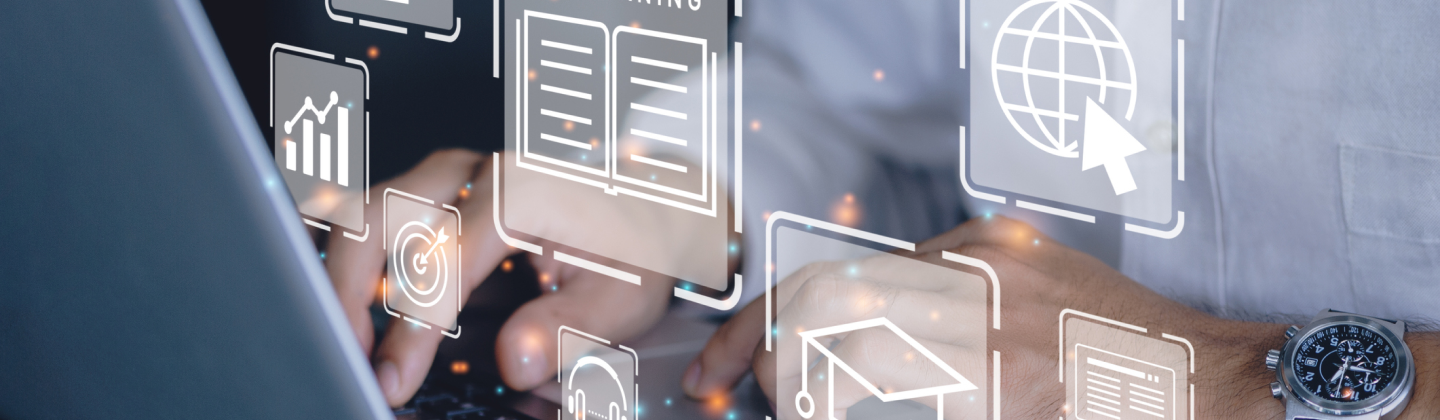
Episode 7: Validation and Verification of Metal Detectors and X-rays
Episode 7: Validation and Verification of Metal Detectors and X-rays
You are watching the seventh video in Kellerman Consulting’s video series on validation and verification in manufacturing operations. In our previous episodes we reviewed how to validate equipment in production settings, and to link validation to verification records each time operations occur.
One type of equipment is uniquely difficult to apply the concepts of validation and verification to, and that is x-rays and metal detectors. There is good reason for the confusion as a result of how this equipment functions, and how they are commonly treated in manufacturing operations. In order to understand how to properly validate a metal detector or x-ray, we need to first explain the challenges.
Controversy About X-Rays and Metal Detectors
Metal detectors and x-rays are commonly considered critical safety equipment in production and retail operations, and certifying bodies for GMP and GFSI audits require them as a part of operation. Wherever metal detectors and x-rays are required, they are usually designated as critical control points, which have special requirements for validation as part of HACCP or preventive controls.
But there is a problem with this, namely that metal detectors and x-rays are not critical control points as defined by Codex Alimentarius principles. The reason for this is because metal detectors and x-rays are only capable of monitoring for foreign materials and are not capable of preventing or removing those objects from getting into the process in the same way that a sieve or filter does .
Because metal detectors and x-rays are not barriers, validating their capability to identify foreign materials is not as clear as validation of measurements such as time and temperature. As a result, there are many different interpretations in the industry and there tends to be a lot of confusion.
Issues with Foreign Material Monitoring Equipment
To add to the confusion in attempting to validate metal detectors and x-rays, the equipment is often very temperamental and frequently malfunctions in operations, resulting in false positives.
When false positives occur, there are simple practices most facilities use to evaluate potentially affected products, such as running through an alternate machine on site, but this also ignores the fact that any false positives are invalidating, and demonstrates a possible larger issue for the foreign material monitoring equipment.
Because the use of metal detectors and x-rays is considered to be an industry standard and best practice, the fact that they are neither traditional critical control points, nor capable of consistently functioning correctly in many operations is almost always left unaddressed by regulators, auditors, customers and other stakeholders.
So as long as foreign material complaints are reduced to acceptable levels, the process is considered to be successful and because of this, we need to validate this equipment as best as we can.
Validation and Verification for Metal Detectors and X-rays
The practice of checking a metal detector or x-ray is performed by placing a sample foreign object on the conveyor system, running it through the aperture and confirming that the machine properly identifies the object and rejects it, which both proves that the machine is working and that it is functioning as intended each time we check it.
Simply said, we are performing both validation and verification each time we do a metal detector check. Kellerman Consulting has noticed many facilities will run test wands through the aperture alone. It is important to note, this is not appropriate for either validation or verification since it does not demonstrate that the metal detector or x-ray can find the object in the actual product, only that it can find the metal by itself.
With that in mind, how we perform the check and how we document the check can be the difference between defining the action as either validation or verification. As we discussed in episode 5, validating a critical piece of equipment is performed by creating a validation report. Since metal detectors and x-rays are so confusing when it comes to validation and verification, it is very important to have a validation report for this equipment. For operations that run wands through 20 or 50 times in a row to prove validation, you can stop doing that, as this is not really a validation exercise. It’s just checking the equipment a bunch of times in a row.
Best Practice for Validation and Verification of Metal Detectors and X-Rays
What we should see as part of validating metal detectors and x-rays is a report with a defined time period, the persons responsible for validating a metal detector, and the operators involved. Next, we need to select the production material that is most difficult to metal detect and x-ray, which is usually the most dense product, or most frequent product that we are going to perform checks on as proof of validation.
For the purposes of a validation report, the test piece should be placed inside representative packaging with either finished product or a substance that is equivalent in density to our finished product, and then run through the detection equipment. The best practice for validation is to rotate the package and try running it through the detection equipment on different sides, or move the test piece around inside the packaging to different locations. That would be toward the top of the packaging, towards the bottom, and then different sides within the finished packaging.
By doing this exercise and documenting that the equipment could find the test piece all throughout the inside of the packaging, we are validating that we have the correct detection device for the products in the facility. Normal verification practices of placing the test piece under product on the conveyor during equipment checks can be done on a daily basis once we have the validation report to reference.
Validation Reports
Creating a validation report each time a new product is added to a line with a metal detector or x-ray should also be documented, and all of the validation reports should be reviewed annually to make sure they are up to date.
We also should have a review of metal detection or x-ray logs for part of the year to demonstrate that the equipment is working on a regular basis, and we can compare that review to the review of the validation reports we have for the metal detector or x-ray as a complete validation and verification program for those devices.
Free Validation & Verification Assessment Log Download
If you would like to discuss having Kellerman Consulting write and implement your food safety and quality management system program, contact us for a free consultation.
Validation & Verification Resources
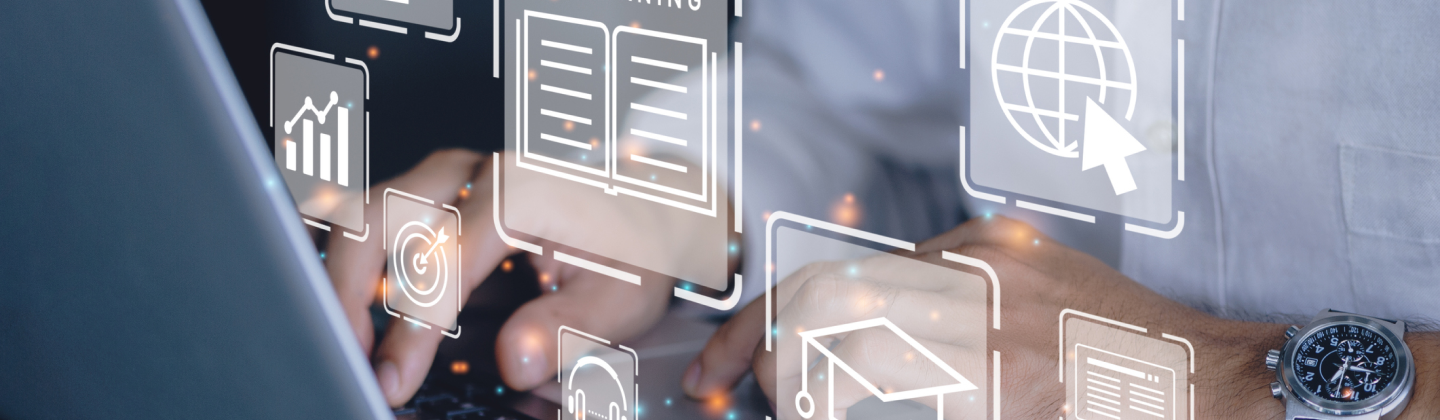