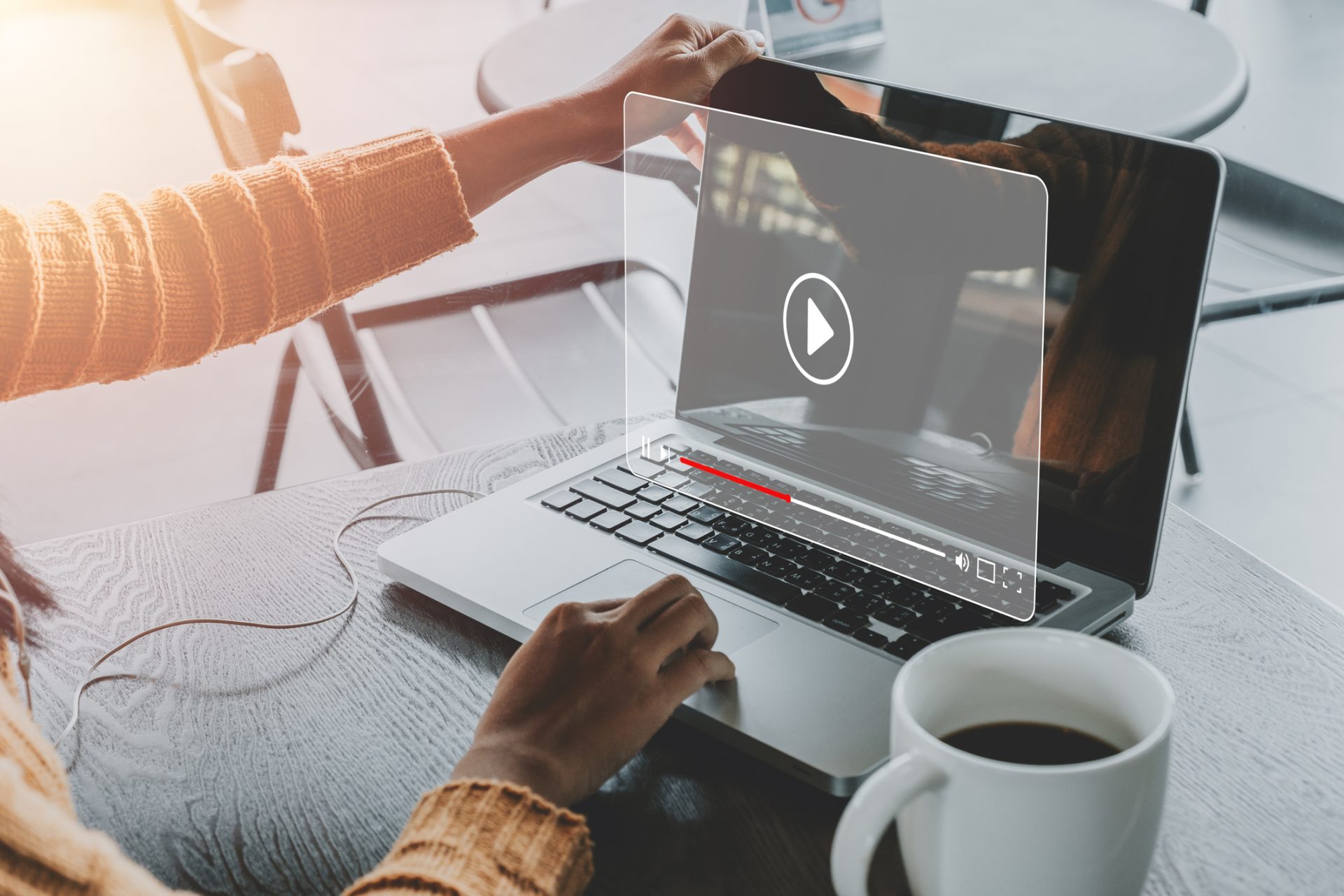
Food Safety Training Videos and Free Downloads
Corrective & Preventive Action (CAPA) Video Series & Related Free Resources
In our Corrective Action & Preventive Action (CAPA) video series, the Kellerman Consulting team focuses on the important topic of Corrective Actions and Preventive Actions, or CAPA. In this seven video series, we cover topics including how to conduct a root cause analysis, the difference between ‘corrections’ and ‘corrective actions’, why documenting loss of control events is so critical, and more. In the first video of the series, we start with describing different types of problematic events in the facility.
Corrective & Preventive Action (CAPA) Free Downloads
In a functional CAPA program, a root cause analysis is an investigation into the source, or root cause, of the deviation. Using tools such as a fishbone diagram or 5-Whys exercise can assist an organization in identifying the true root cause of the non-conformance. Hold and release procedures are an important aspect of a functional CAPA program. A Hold Tag (with common hold codes) and a Hold & Release Log can streamline a site’s process for identifying and releasing quarantined items.
Root Cause Analysis Download
Use this Root Cause Analysis Form (based on the 5-Why Method) to assist your team in investigating the root cause of a nonconformance and documenting the follow up actions to ensure effectiveness.
Hold and Release Log
Use this Hold & Release Log to document the status of products, equipment, or materials placed on hold, as well as the justification for releasing or rejecting quarantined items.
Hold Tag With Codes
A Hold Tag is used to identify products, equipment, or materials that are placed on hold while pending a CAPA investigation. The use of Hold Classification Codes eliminates confusion around why the item is quarantined
Fishbone Diagram
A Fishbone Diagram is a great tool for determining or identifying the root cause of a deviation by looking at various angles of potential causes.
Questions about costs, timelines and requirements?
Contact Us Today for a Free Consultation
Available to travel for your project
-
Headquarters
-
Offices