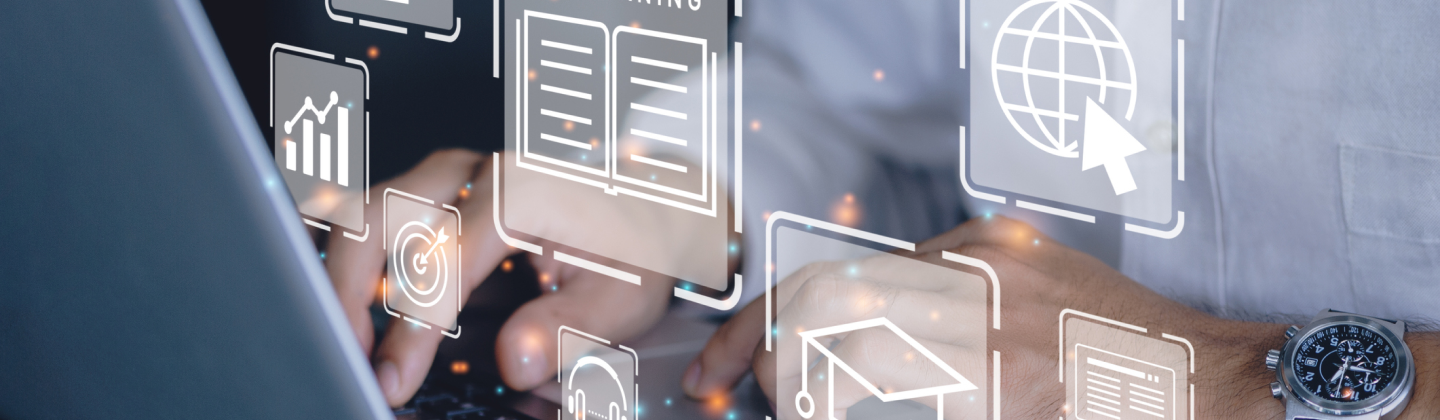
Ep 3: Critical Quality Metrics and Key Performance Indicators
Ep 3: Critical Quality Metrics and Key Performance Indicators
In this episode we are going to focus on the verification concepts within operations that are used in complex quality management systems, namely critical quality metrics and key performance indicators used to monitor processes and verify the effectiveness of the quality management system.
In order to properly tie these two types of quality assessments to the ideas of QA and QC, we will be examining quality metrics and key performance indicators through the lens of quality assurance and/or quality control.
First we are going to start by defining what a critical quality metric is within a quality management system, and which employees should be evaluating these.
Critical Quality Metrics Within a Quality Management System
As we think about quality as the conforming end products or services, we should be able to identify the specific process steps or conditions by which we have achieved that quality.
For an automotive engine part, that may be the correct diameter and thickness to fit the specified engine of our customer. For an IT security company, that may be the correct coding to protect backdoor access of a website against a newly identified virus or hacking threat. In both of these examples, the metric would be the conforming quality of the product or service to meet its designed function.
In all of these examples, we have measurable aspects that can be checked by a quality associate or lead in real time to confirm that the system in place is resulting in that quality we expect.
At Kellerman Consulting, our critical metric is the presence of the correct documents to match our contracts and projects with our clients. We also have a critical metric of scheduling and showing up to our implementation meetings with clients once the documents have been delivered.
The quality checks for these metrics are achieved when management reviews project documents and the status updates from the consultants on where implementation has progressed to.
We expect all of our projects to be completed successfully when the correct documents are provided to our clients, and when we have facilitated the necessary follow up meetings and updates to those documents prior to a scheduled audit or customer request.
Performing the Critical Quality Metric Check
Because we are defining the critical quality metric as one or more actions that must be made accurately during operations resulting in the conforming product or service, the check must be performed prior to completion or release.
A common question we get from our clients is, “How many checks are we supposed to do”? The frequency and number of checks is determined by the quality team in your organization based on risk, the type of check being performed, and it’s influenced by your run size and a variety of other factors. If you aren’t sure how many checks to do, then this can best be decided by collaborating with your team.
A paper or electronic form should be in place that defines the critical quality metric, the correct specification for the metric being checked, and the results of the check. Additionally, the personnel conducting the check must understand how the check is representative of the larger operation.
Because it is impractical to check every product on a line, or review every service event, it is important that the recorded forms provide sufficient data so that the quality control group and top management are able to get a complete picture of the effectiveness of operations based on the frequency of the checks and the information recorded.
The frequency of checks may be changed after careful re-evaluation of the program. Process improvements may lead to a reduced frequency of checks, and on the other hand, increased issues identified in the process may lead to increased checks.
Key Performance Indicators Within a Quality Management System
Key performance indicators, or KPIs, are similar to critical quality metrics in that they are recorded data used to determine if operations are functioning correctly.
However, unlike the critical quality metrics we have discussed, key performance indicators are higher level checks of the quality management system that are focused not necessarily on specific checks on the line, but rather overall outcomes of the system.
Where our quality control checks of critical metrics prove operations are working correctly during operations, the key performance indicator should focus on the larger collection of data that prove the overall system works.
When setting a key performance indicator, leadership should identify the aspects of operations that cannot or should not ever be out of conformance. Key performance can also be drivers of improvement and business goals.
And since key performance indicator reviews are higher level evaluations and should have some sophistication in trending analysis, where we previously assigned quality control checks to operators or QC personnel, key performance indicators of the system should be controlled by individuals capable of compiling data, analyzing data and presenting data to top management, which is typically a Quality Assurance Manager or a member of Top Management.
When and How to Perform Key Performance Indicator Reviews
We generally don’t need to present every quality check to top management, and it would cause frustration and be an inefficient use of operational and managements time to do so. Similarly, we do not need to evaluate key performance indicators on a daily, or even weekly basis when operations are set up and running correctly.
Instead, we should have either monthly or quarterly reviews of these metrics that allow top management, key decision makers, quality assurance and quality control personnel to understand the direction of the organization, potential changes needed to improve deficiencies found within the quality management system, and upcoming events that may result in changes to key performance indicators themselves, or where we are going to change the metrics for existing KPIs.
Combining QC Checks, QA Programs & KPIs
When we combine quality control checks, quality assurance programs, with the key performance indicators, we have the actions of a fully functional quality management system.
When we examine the combined critical quality metric checks for QC and the key performance indicators for the program, we should see that we are checking the main pressure points of our Quality management system, even as this does not require that we are examining all of the documents and forms used to manage operations.
In our next episode, we are going to look at Training for the Quality Management Systems, and trainings for Quality Control and Quality Assurance.
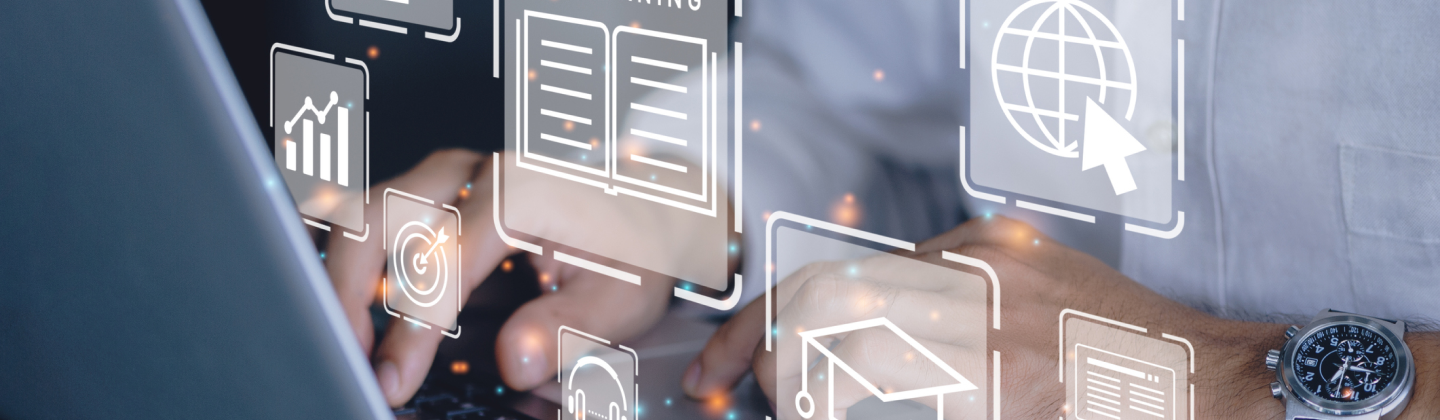