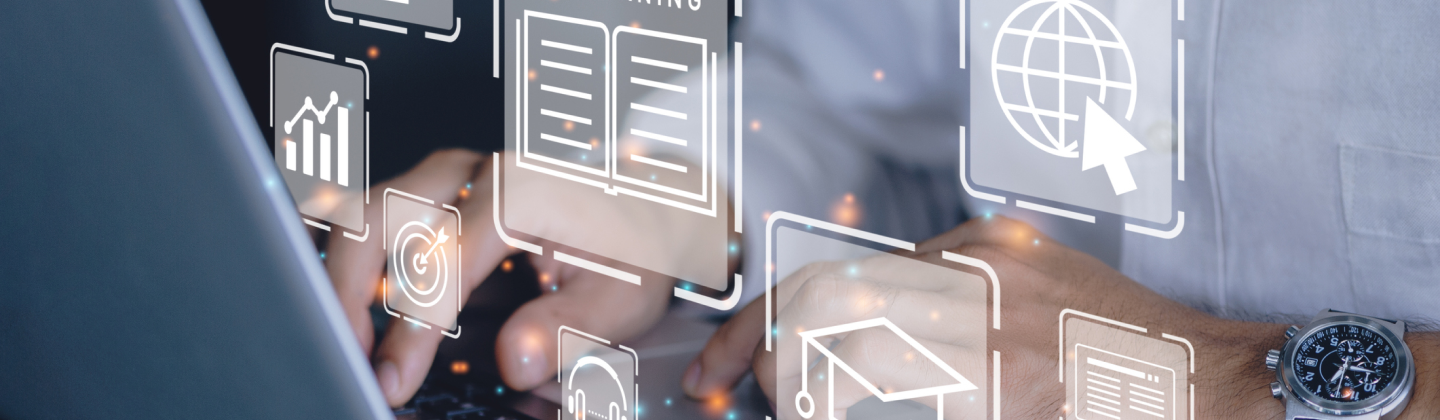
Episode 5: Worker Safety and Chemical Control
Episode 5: Worker Safety and Chemical Control
Preventive Maintenance & Repair
In this episode we are going to review some basics in chemical control and worker safety practices for maintenance and repair, and how to enforce those in the safety and quality management system.
Regulations for chemical control come from the Environmental Protection Agency, and worker safety regulations are published and enforced by the Occupational Hazard and Safety Administration.
When determining if maintenance and repair activities meet regulatory standards in a safety and quality system, the organization is responsible to make sure that employees are handling their actions, and the use of chemicals in compliance within the regulations of those entities.
We are first concerned with preventing workers from being in a position where they are acting in an unsafe manner while performing their job duties. Secondly, we are concerned with preventing employees from willingly putting themselves and others in unsafe situations.
Management must do all it can to enforce worker safety rules, including firm disciplinary actions where workers feel that required worker safety actions don’t apply to them, regardless of the reason.
When we look at the likelihood of injury and violations of worker safety involving maintenance and repairs, we have to be more concerned with actions around repair than we are with preventive maintenance.
Although problems can and do arise around disabling or overriding system protections in any maintenance and repair action, preventive maintenance actions are often conducted during non-operational times, and the employee may be less vigilant when working on non-functioning equipment.
When working on functional equipment during off hours, it is imperative to continue to follow all employee safety practices. When employees choose to not follow mandatory safety precautions, these situations should be addressed as a safety or behavioral issue, often through safety training and robust supervision of problematic employees or contractors.
As a general rule, locking out of equipment should always be practiced on equipment requiring repair, regardless of the presumed status of the equipment.
For the use of chemicals in all operations, including maintenance and repair, it is critical that all chemicals are controlled. Meaning there are specific storage locations and certain chemicals may only be used in certain areas. When chemicals are transferred to other containers those containers must be labeled properly. Frequently, chemical usage in facilities is treated in the same way they are at home, and this is not acceptable.
A record of all chemicals in operations, and their intended use should be in place, and checked regularly to make sure it is up to date. Safety Data Sheets for every chemical in the facility should be kept in an easily accessible location in case of an emergency involving the chemical such as someone swallowing a chemical, getting a chemical in their eyes or nose, or otherwise getting a dangerous chemical on their skin.
The maintenance area may have a separate storage area and list of chemicals from other operations, and this is acceptable as long as there is good control of both the storage and chemical lists. For food facilities using chemicals, food grade chemicals must be separated from non-food grade chemicals.
In our next episode, we are going to look at ISO and GFSI requirements for preventive maintenance and repair.
Thank you for watching. For free downloads to accompany this video series, visit the free training videos & resources page of our website.
Subscribe to our YouTube channel or follow us on LinkedIn to be notified of new educational food safety resources.
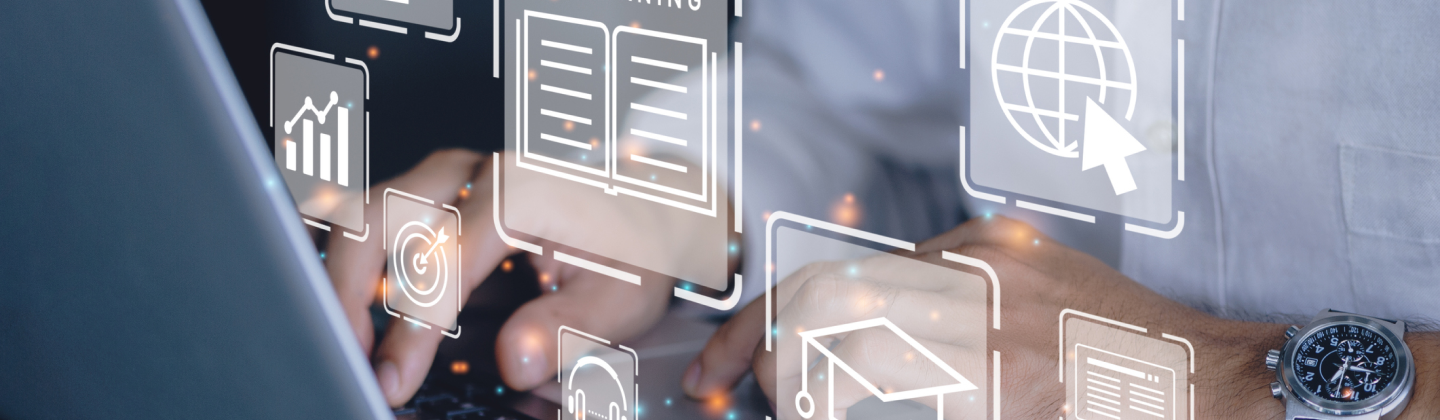