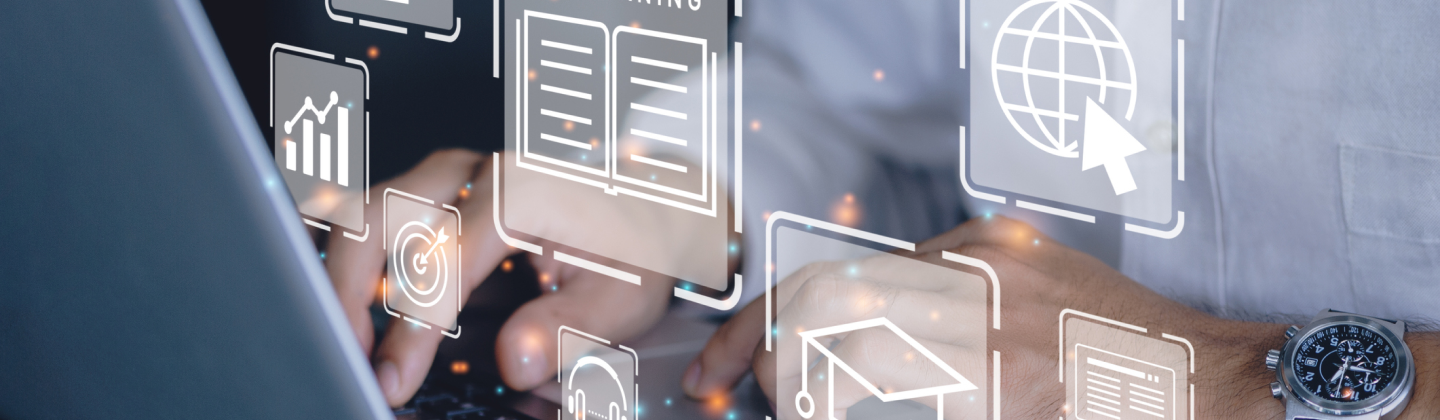
Episode 3: Documenting Non-Conformances, Root Cause Analyses, Corrections, Corrective Actions, and Preventive Actions
Episode 3: Documenting Non-Conformances, Root Cause Analyses, Corrections, Corrective Actions, and Preventive Actions
Corrective & Preventive Actions (CAPA)
In Kellerman Consulting’s third episode of the CAPA video series, we talk about how to properly document a root cause analysis investigation, corrections, corrective actions, and preventive actions. Additionally, we review why proper documentation of a CAPA program, and the communication of these events are so critical to an organization’s food safety culture.
When documenting the details of a deviation or nonconformance, begin by capturing both when the deviation occurred (if known), as well as when the deviation was discovered. This is important to understand, because if a deviation occurred at 7:00am, but wasn’t discovered until 12:00pm, the amount of product impacted by the error will likely be greater than if the deviation was discovered only an hour after it occurred. It is also important to include who discovered the deviation so that we can collect additional details about the event, if necessary.
We must also document what policy, procedure, or work instruction was violated or impacted by the deviation. This allows us to determine if changes or updates are needed to these procedures to prevent future occurrence of the deviation. For example, if the deviation involved the discovery of an unlocked dock door, we should evaluate whether our shipping and receiving security policy includes the step of locking dock doors at the end of a shift.
Documenting the details of a root cause analysis, as well as the corrective and preventive actions of a nonconformance event is important for many reasons. First, when we succeed in resolving these issues, we prove to ourselves and our employees that we are capable of both identifying and correcting problems when they occur. We can also demonstrate this resolution and improvement of issues to outside reviewers, such as auditors, customers, or regulatory authorities. Second, documenting nonconformances over a period of time (i.e. monthly, quarterly, or annually) allows us to see trends in the amount or type of deviations experienced within the facility, and helps us to evaluate whether we are improving or declining in our operational performance.
In our next video in the CAPA series, we discuss deviations involving key metrics. Subscribe to our YouTube channel or follow us on LinkedIn to be notified of new educational food safety resources.
Watch the CAPA Video Series & Download Related Free Resources
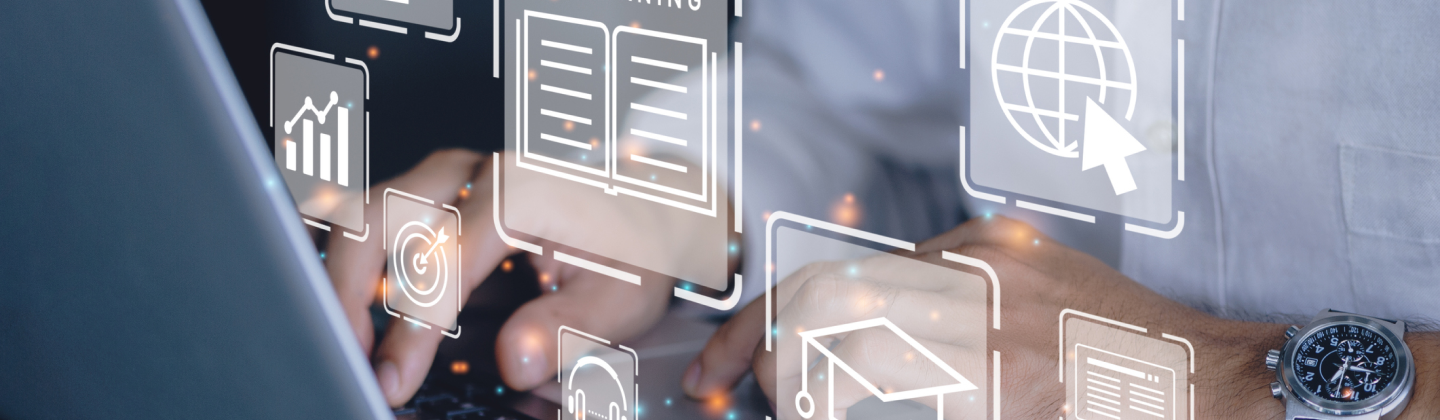