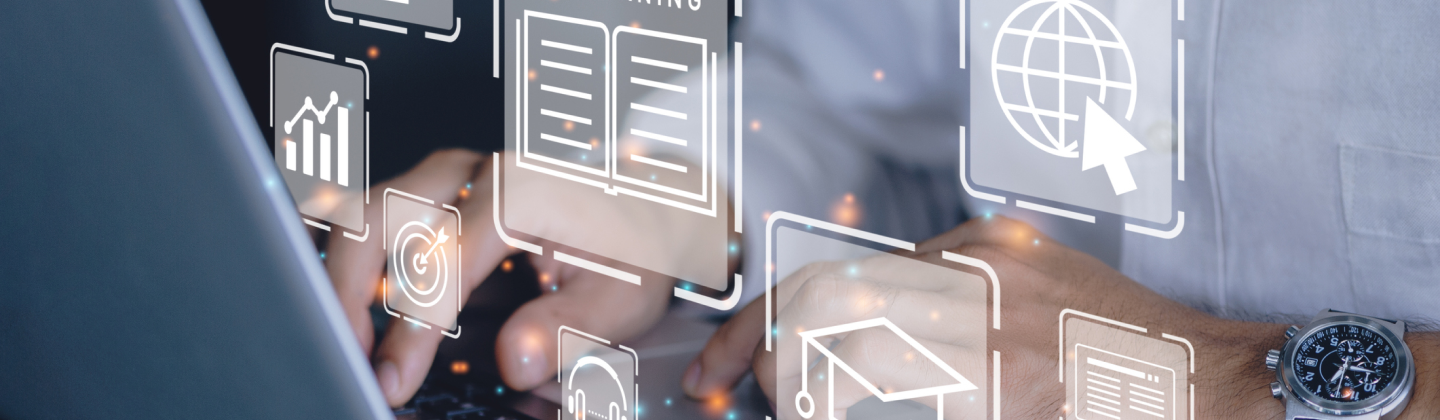
Episode 6: Preventive Maintenance and Repair in Quality and Safety Certification Programs
Episode 6: Preventive Maintenance and Repair in Quality and Safety Certification Programs
Preventive Maintenance & Repair
You are watching Kellerman Consulting’s video series on maintenance and repair, and in this video we are going to focus on the Quality Management System and GFSI requirements for those activities.
ISO is a quality management system audit applicable for any organization and can be applied to most products and services across industries.
GFSI is the Global Food Safety Initiative, an international organization that publishes requirements for food safety programs to adopt when those safety programs want to be benchmarked to GFSI.
ISO quality management requirements and GFSI programs operate on many similar programs, and all programs have a requirement to control maintenance activities and repair of the facility and equipment.
Maintenance and repair are not mandatory activities for quality and safety programs, and organizations without physical equipment or facilities would not be expected to engage in either practice. Auditors will also examine any maintenance areas, tool boxes in the facility, chemicals used for operations and record keeping such as work orders and schedules for maintenance and repair activities.
If an auditor finds unacceptable conditions as they define it, uncontrolled or temporary repairs and uncontrolled chemicals, they may issue minor or major violations. Additionally, calibration records and monitoring records for assessment of equipment and the facility for signs of wear or damage are expected. Repair and maintenance records should correspond with any findings noted during facility monitoring.
For ISO and GFSI Programs, our videos do not directly address specific clauses for maintenance and repair, but if you take the comprehensive approach to internal audits and walkthroughs in sections, they will meet or exceed these standards. Please do not rely solely on our recommended program, and make sure your program references and meets all certification clauses in preparation for your audit.
For ISO, maintenance and repair requirements are tied to clause 7.1.3 for infrastructure as well as measuring and monitoring devices in clause 7.1.5. As with all requirements in ISO, the requirements are very vague so as to apply to all possible facilities, and the information for maintenance and repair are up to the facility to determine and document.
One important concept to note is the traceability of measuring devices, which is the terminology for calibration of instruments. So it is important to read clause 7.1.5.2 carefully as part of the development of the preventive maintenance practices in the facility. Personnel responsible for maintenance and repair must have undergone appropriate training, and proficiency evaluation of their work must be done at least every year to demonstrate competency. Top management must confirm that the maintenance and repair activities are performed regularly to keep the infrastructure in good condition, and any maintenance and repairs conducted as part of a corrective action are performed in a reasonable amount of time and are effective. Lastly, communication of maintenance and repair, and review of external providers, post operational actions and feedback should be included in any ISO maintenance programs.
For SQF Edition 9, requirements for maintenance and repair are found in the GMP modules for each book. In the module for food manufacturers, it would be 11.2.1 in the site operations section of the SQF Safety Code manual in section.
The SQF Practitioner and the backup are expected to have undergone food safety training through a HACCP training course, as well as PCQI food safety training in FSMA complaint facilities to qualify them to oversee the safety of maintenance and repair. The practitioner must at a minimum sign off that maintenance and repair actions are documented, and that they were scheduled.
Additionally, all temporary repairs must have documentation proving they are planned to be made permanent, and the practitioner is responsible for following up to make sure that those permanent repairs were completed as scheduled.
Cleaning and tool removal is required to be documented for each repair, and regular GMP inspections are expected to include review of maintenance and repair activities and Internal auditing must include review of records for maintenance and repair at least once per year.
In all cases, the food safety trained person or persons must oversee the document-controlled non-conformance reports where maintenance and repairs are a required corrective action, and separately, those persons must oversee the non-conformance reports when there is a non-conformance in the maintenance and repair practices themselves.
For BRCGS programs, the Issue 9 requirements as of March 2023 are located throughout the site standards found in section 4. Starting with the requirement that floors are in good repair, and continuing with section 4.7, the maintenance program is expected to be fully scheduled, documented, and analyzed for trends. We strongly recommend the use of an electronic scheduling and record keeping program for maintenance in a BRCGS facility.
Training requirements for a BRCGS Safety Lead are HACCP training, PCQI training for FDA regulated facilities, and the ability to demonstrate full oversight of the maintenance and repair to assess its ability to maintain quality and safety standards.
It is the expectation of the BRCGS program that maintenance and repair prevent equipment breakdown, and so the emphasis on preventive maintenance should be clear as part of the Culture of Quality and Safety, and the preventive maintenance schedule and activities should be included in the monthly program review.
BRCGS focuses strongly on foreign object and foreign material controls, so the maintenance and repair program should include actions taken to prevent tool loss such as a 5-S program and itemizing all tools where possible, including etching.
The leader of a BRCGS program may delegate oversight responsibilities of the maintenance and repair program, but final assessment of the program and the effectiveness of maintenance and repair must be performed by the lead.
Additionally, one of the four internal audits each year must include review of maintenance and repair documentation as well as review of all corrective actions where maintenance and repair occurred, as well as corrective actions in the maintenance and repair program.
For FSSC 22000, we see similar to the requirements in ISO, with maintenance and repair requirements are again tied to clause 7.1.3 for infrastructure. All of the remaining requirements specific to maintenance and repair are found in the ISO 22002 Technical Specification manual for the type of facility under certification. For food manufacturing facilities, maintenance requirements are found in section 8 of the 22002-1 manual, and these include a preventive maintenance schedule for all equipment associated with food hazards, addressing of temporary repairs and adequate training of all maintenance personnel. For food packaging companies, the ISO 22002-4 manual has these requirements in section 4.5.4.
ISO programs emphasize evaluating the competency of employees involved in the program, and as with ISO programs, proficiency evaluation of maintenance work must be done as part of the training program. Top management must confirm that the maintenance and repair are performed in a way that assures food safety and should include review of external providers, post operational actions and reviews of customer complaints where maintenance and repair may be a root cause.
Finally, communication of maintenance and repair, corrective actions where maintenance and repair are included, corrective actions for the maintenance and repair program and how these actions affect the food safety program and the control of hazards.
For PrimusGFS, section 5.14.01 through 5.14.13 of Module 5 of the GMP section for pack house and warehousing addresses maintenance along with sanitation.
The food safety management system in module 1 and the GMPs for indoor and outdoor agriculture, including farm crews, only reference things like drains and equipment design allowing for repair.
The repair and maintenance requirements in Module 5 require logs for maintenance and repair, as well as documented filter changes to air conditioning and coolers. Primus programs must also include training logs for maintenance and repair personnel, as well as calibration and preventive maintenance logs and schedules for equipment if the facility chooses to use those.
Thank you for watching. For free downloads to accompany this video series, visit the free training videos & resources page of our website.
Subscribe to our YouTube channel or follow us on LinkedIn to be notified of new educational food safety resources.
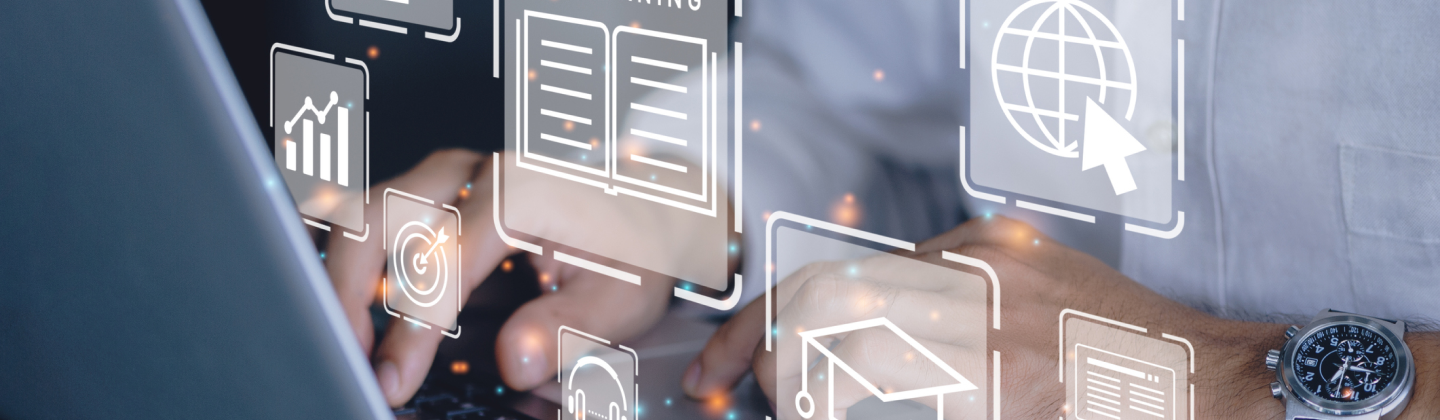