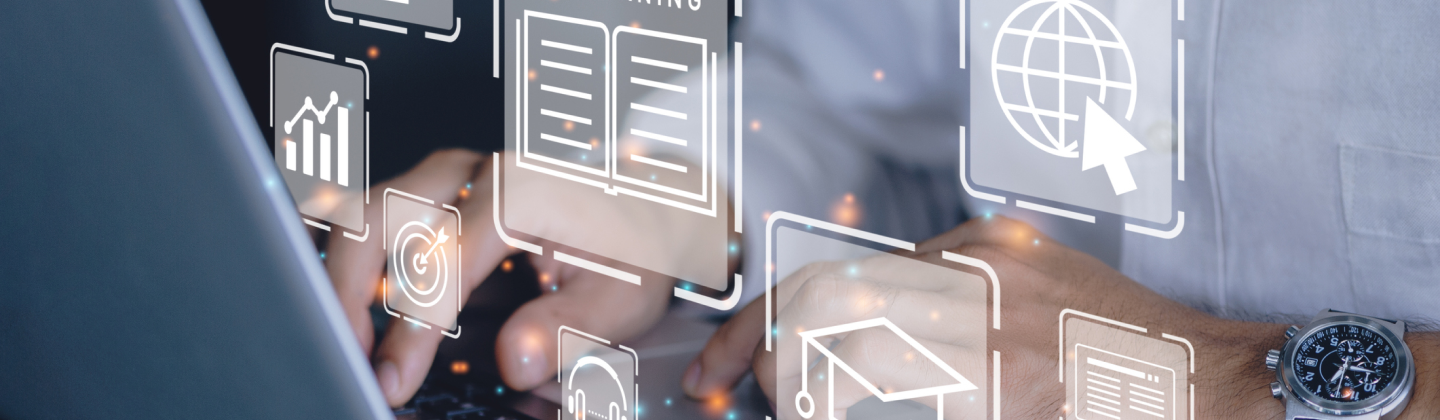
Episode 1: Introducing Validation and Verification
Episode 1: Introducing Validation and Verification
In Kellerman Consulting’s Quality & Food Safety Training series on validation and verification, we examine what validation and verification means for the entire company and how to apply these concepts in practice. We explore what validation and verification means for ISO Quality Management Systems and Global Food Safety Initiative (GFSI) Food Safety and Quality programs. We will look at the critical safety and quality steps associated with the operations of these types of programs.
Definition of Validation & Verification
The concepts of validation vs. verification are commonly confused. During the course of this video series we will clarify these topics using examples from our experience in food safety & quality assurance and we will explain the differences between validation and verification.
To put it simply, to Validate is to approve, certify or endorse and to verify is to check or demonstrate.
Our hope in producing these videos is to demystify and explain how to perform verification actions within a facility, and how to determine if a valid program is adequately monitored with accurate records each time operations are performed.
We are confident that by the end of this video series, you will have the tools needed to adequately validate your facility, your programs, and supporting actions, as well as the knowledge to properly verify these programs through monitoring and record keeping.
To start we are going to define what validation and verification are, and the most important concepts for each.
How Validation is Achieved
To understand the concept of validation we must focus on the conditions necessary for something to work properly.
For a business, validation is achieved when systems and operations are confirmed as functioning in a correct way. Within all operations, the need for validation of the program is essential.
This validation may be considered achieved based on revenue or profits, days without a worker accident, by hitting safety or quality milestones in product, through testing, or direct observation compared to work instructions.
Validation statements or assessments are often a requirement from a client, a government regulator or an auditor to provide proof of validation, and this is the source of confusion.
Because validation is the documented proof that the operational system is capable of achieving its intended outcome, it can be confusing where to start for validation, especially in long running businesses that have not historically validated their programs or systems.
In our later episodes we will explain how to document validation of all or part of the programs.
Verification vs. Validation
Once we have established the conditions or actions required for a facility or program to work properly, we must maintain evidence that these conditions were met each time operations was performed
This is what we call verification, and we can more easily point to what verification is due to the fact that it is demonstrated through monitoring records.
Verification may include weight checks on scales, temperature checks for refrigerators or ovens, metal detection checks, label checks, cleaning and sanitation records and/or calibration records.
In all of these written checks, an employee is confirming that the system works as defined by work instructions.
It is common for employees to mistake verification activities used to confirm processes following proper action for validation with validation itself.
An example of this would be a slicing machine that is capable of cutting product correctly. Validation is that the correct machine is in use with the correct blade and correct safeguards, and this validation would be performed when the machine is purchased, or when the materials are first used in the slicing machine. Verification is measurements of the cuts to show that the slices are of the correct length and pattern.
To further help clarify the difference between validation and verification, we can look at who is responsible for each process.
Who is Responsible for Validation?
Creating a valid operation within a facility is done through strategic and logistical planning, and must be headed by the company leadership, with technical and financial support from management.
In a properly running business, validation comes from the top of the organizational chart and is communicated downward to support staff through effective training, schedules, maps, process flows and registries.
Information crucial to validation are projections of needed equipment, required space and time to complete tasks, the size and quantities of materials to be handled, processed and shipped, and the number of employees or machines needed to run operations during each shift.
Also needed for validation is scientific data on the conditions needed to maintain the safety and quality of inputs and outputs of operations.The Senior Management, along with architects, engineers, scientists, regulatory guidance documents, and subject matter experts are the source of process validation.
When Does Validation & Verification Need to Occur?
Proper validation is planned prior to the commissioning of a new facility, or prior to the start of a new task within an existing facility. Market research, business plans, cost projections, lab tests, and trial runs are all actions that should be associated with validation.
Validation is generally expected to be confirmed during the months following the start of a new facility or process, and this often refers to a validation time period, with 90 days being a good baseline for planning purposes.
Processes should be re-validated whenever a process changes, or at a minimum annually, to meet regulatory and GFSI/ISO requirements. A revalidation can be as simple as checking for updated scientific information, new regulatory guidelines, or reviewing trends in your own records.
After validation planning, and during startup and validation time periods, verification activities are performed to monitor both progress and planning, and provide the information needed to adjust validation when it inevitably fails to account for all variables.
Who is Responsible for Verification?
Verification is performed by positions such as technicians, equipment operators, warehouse employees, maintenance, cleaning and sanitation staff, Quality Assurance or Quality Control, security guards, purchasers and other administrators.
That is to say, unlike validation, verification comes from the lower levels of the org chart and the information trickles its way upward through management review, internal audits and self-inspections of training materials, receipts, reports and work records.
Other critical sources of verification are emails, text messages, internal message boards and meeting minutes where status reports on operations are communicated. If these verification activities sound like the normal actions during the work day for employees, that’s because they are . Verification is ongoing, and makes up the vast majority of common work performed by employees in properly defined jobs.
Free Validation & Verification Assessment Log Download
In our next episode on Validation and Verification, we will focus on examining invalid processes, and incorrect process design.
If you would like to discuss having Kellerman Consulting write and implement your food safety and quality management system program, contact us for a free consultation.
Validation & Verification Resources
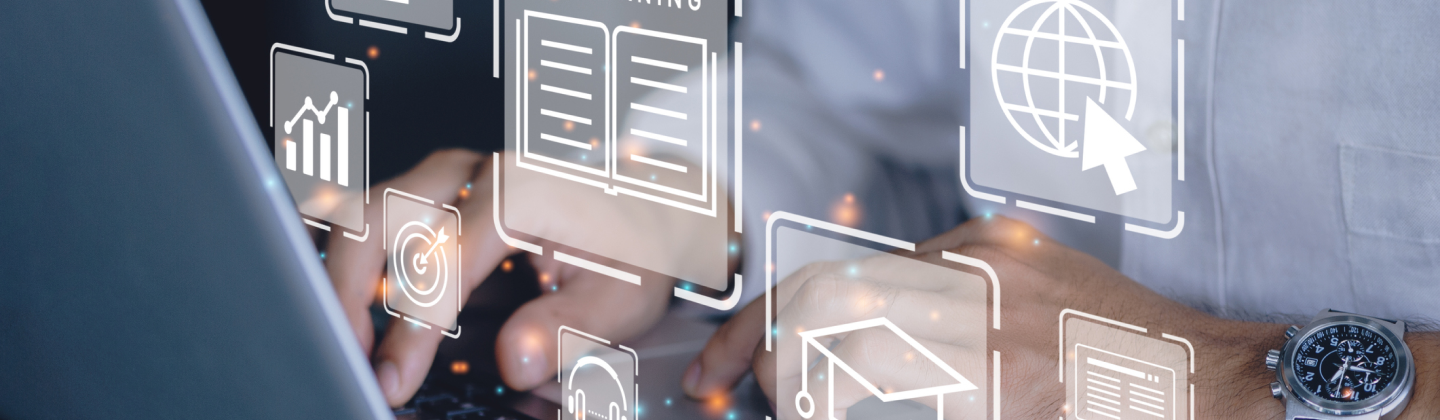