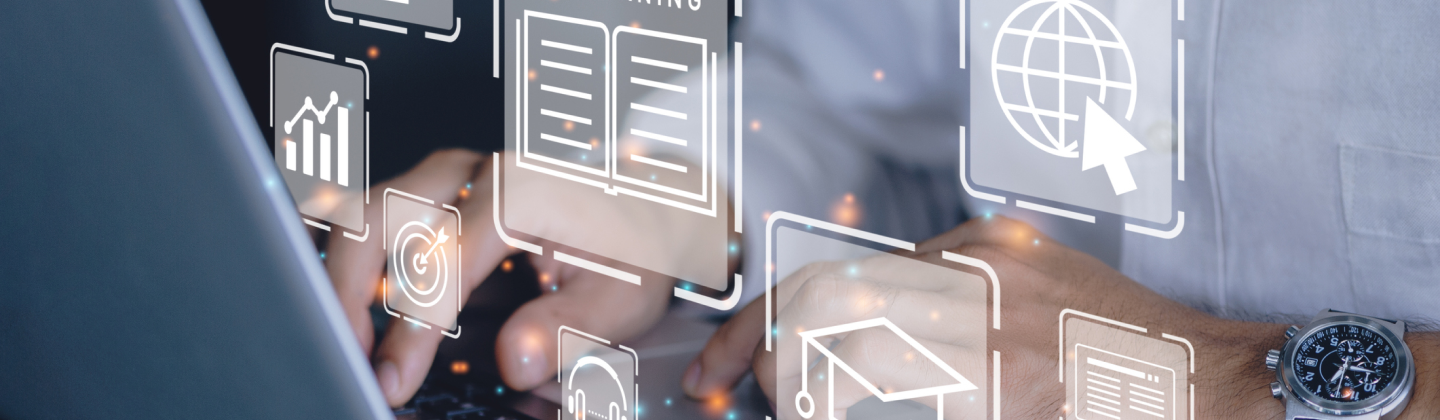
CAPA Webinar Summary
CAPA Webinar Summary
View the free webinar recording on the topic of: “Corrective Action and Preventive Action (CAPA): Addressing Problems in Operations” or read the summary below.
Brian Kellerman, Chief Quality & Food Safety Officer covers:
-
- Identifying Non-conformances
- Classifications of Non-conformances
- Errors and Root-Cause
- Mishaps and Root-Cause
- Anomalies and Root-Cause
- Force-Majeure and Root-Cause
- Root Cause Statement
- 5-why and Fishbone Diagrams
- Corrections and Corrective Actions
- Closing out inspections and audits
Identifying Non-conformances
There are non conformances in your business right now, how are you going to identify them?
We find non-conformances several ways:
- During Normal Operations
- During Inspections of Operation
- During Internal Audits, Second/Third Party Audits (Regulatory Inspections, Customer Audits and Certification Audits)
Non-Conformances fall into three categories:
- Raw Materials and Products
- Operations
- Infrastructure
Classifications of Non-conformances
Here is a way to think of non-conformances found in operations: any non-conformance directly related to outputs must be treated as significant, regardless of which of the categories it may fit into.
Errors and Root-Cause
When a non-conformance is foreseeable and probably (meaning likely to happen), it may only require a correction, but best practice is to include a root cause statement. We will provide an example of a root cause statement later in the presentation.
Error would be bringing the wrong labels to the line (or mislabeling products), failure to comply with procedures, or failure to provide timely service.
Mishaps and Root-Cause
When a non-conformance is unforeseeable but is probable, we need to have a root cause investigation, and it may only have a correction, unless it looks like it could happen again (then it should have a Corrective Action)
This would be a forklift crashing into racking, or a failure to complete repair effectively by a service provider.
Anomalies and Root-Cause
When a non-conformance is foreseeable but is unlikely to happen, we need to have a root cause investigation, as well as a correction and corrective action to watch for these recurring circumstances
This could be a roof cave during an ice storm, or a truck/car crash during transit with finished product in it.
Force-Majeure and Root-Cause
When a non-conformance is neither foreseeable nor likely to happen, we are allowed to write it up as such, one time.
This could be a black out for the locality, or a vehicle running into the building
If it happens a second time, it is no longer Unforeseeable, nor is it Improbable, and it needs to be reclassified as a non-conformance requiring a corrective action (Mishap or Error).
Root Cause Statement
Root cause statements should include the following:
- Non-Conformance Date & Time
- Product (lot codes) /Equipment/Facility Location
- Person(s) Performing Root Cause
- Describe the non-conformance, the cause, and how it was identified: (During Scheduled Operations, During GMP inspection, During Internal Audit, Customer Feedback/Complaint)
- Method of Investigation to the Root Cause: (5 Why, Fishbone, Document Review, Interviews, etc.)
- Can it be determined what actions lead to the the Non-Conformance?: Yes or No.
- Is this a repeat occurrence?: Yes or No.
5-Why and Fishbone Diagrams
These are not required techniques
There are no required methods of Root Cause Analysis
These methods are best for situations where:
1.A critical part of our program has failed, regardless of the reason
2.The reason for why a non-conformance has occurred for unclear reasons
A Free Fishbone Diagram template and A Free Root Cause Analysis template can be found on our website by clicking this link.
Corrections and Corrective Actions
When a non-conformance is found to be a simple error, requiring a quick and immediate fix, then a correction is performed
If the non-conformance is a systemic problem, then a corrective action that addresses the deeper problem is required
Best practice is to create a root cause statement for all non-conformances:
- This should be done where only a correction is performed
- This must be done for all corrective actions
Closing out inspections and audits
Root Cause
Explain the things done to prevent this from happening, followed by why it happened (use “however” or “but”)
Example: The program contained a procedure for Record Control, and the updated record was presented to management on 2/1/25, however, the new revision date was not properly updated on the Record Registry
Correction
How was this fixed during or immediately after the audit
Example: Backflow prevention was performed by plumber on 2/5/25
Corrective Actions
How was the program updated to check for this non-conformance
Example: Self Inspection was updated to include door checks for properly locking and securing
Preventive Action
What actions (usually reviews or trainings) are scheduled to assure that correction and corrective actions remain in place prior to the next inspection/audit
Example: Management Meeting Scheduled for 12/1/25 to review food defense checks and inspection checks performed during the year.
CAPA Webinar Final Thoughts
There should be a root cause statement for all non-conformances, and a statement that an event is not likely to ever happen again in the cases where it is unforeseeable and improbable.
Reviewing all non-conformances at management meetings/reviews is best practice.
You should expect to have several non-conformances for each internal audit performed, and each should have corrections/corrective actions (with the date and person responsible for the actions) and root cause statements.
If you have additional questions or if you would like a free consultation please contact us at (800) 535-1376 or info@kellermanconsulting.com.
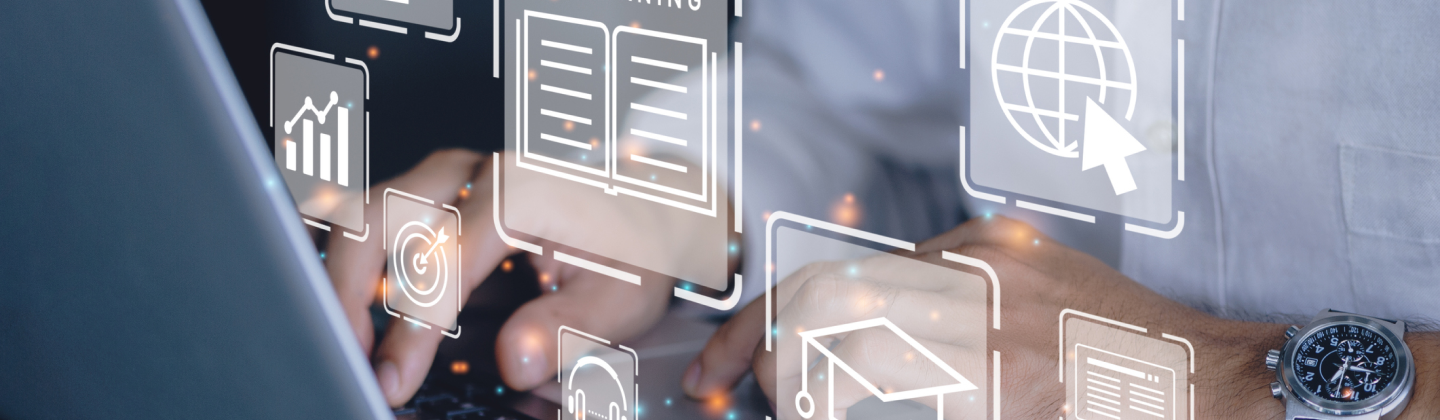